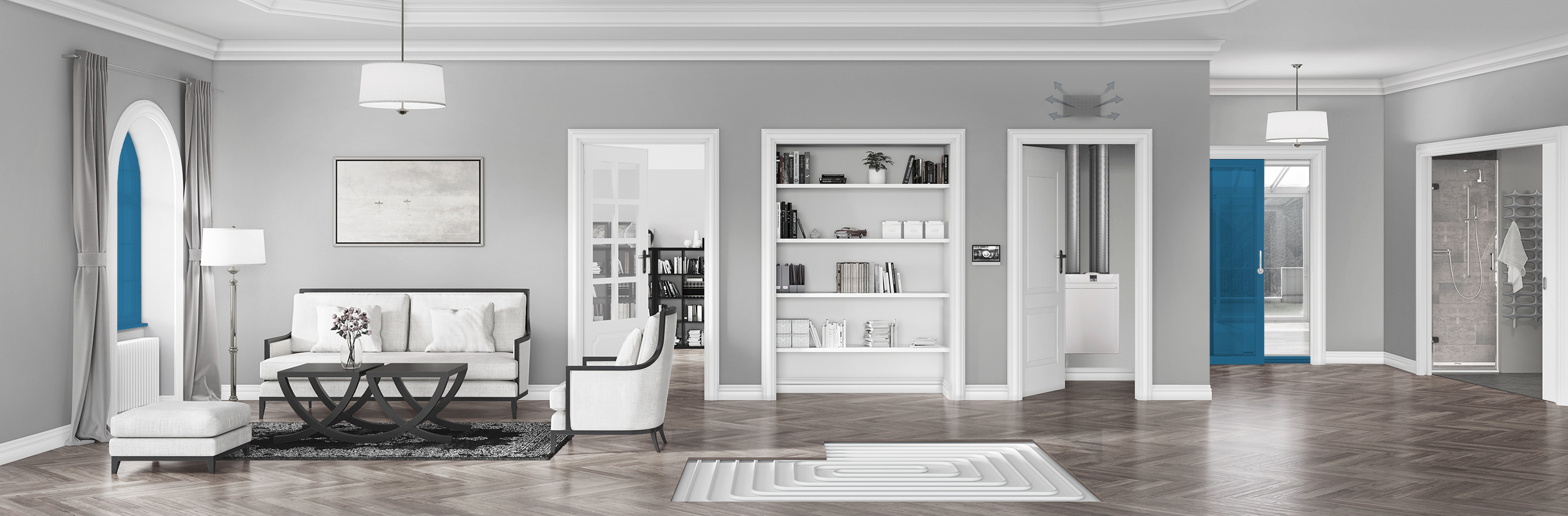
Division
Windows
Market trends
The Windows Division maintained its revenue of CHF 351 million (previous year: CHF 350.8 million) during the reporting year. When adjusted for currency effects, this resulted in an decrease of –1.4%. The EBITDA rose significantly from CHF 8.2 million to CHF 29.7 million. This was achieved in spite of the negative impact of increases in the CHF-EUR exchange rate, which had an adverse effect on the result as well as the ramp-up and conversion costs for ongoing transformation projects, due to production within the euro zone and the high proportion of sales in Switzerland. Without special effects, the EBITDA grew from CHF 7.6 million to CHF 13.3 million. The EBIT improved from CHF –5 million in the previous year to CHF 15 million, or without special effects from CHF –5.9 million in the previous year to CHF –1.4 million.
EgoKiefer successfully raised its volume of incoming orders in 2017. In comparison to the previous year, this resulted in an increase of around 5%. This positive trend has increased order volumes for the beginning of 2018 and will be reflected in revenues throughout the course of the year. With the launch of the new generation of wood/aluminium windows, the new vinyl and vinyl/aluminium lift-and-slide doors, and the wood and wood/aluminium front doors, the product range received a major boost in terms of strength. Combined with its new vinyl and vinyl/aluminium windows, which were showcased at Swissbau 2018 and are due to go on sale in the second quarter of 2018, EgoKiefer has further enhanced the competitiveness of its range. In addition to these new products, the company also underwent a rebranding process and launched the “EgoKiefer Academy”. The new academy is used to provide specialist trade partners and employees with ongoing professional development so that customers can receive even better support with their building projects.
The strong economic growth, good prospects on the labour market, and declining unemployment in Poland had a very positive impact on the housing market. Dobroplast benefited from this trend as a result and was able to increase its revenue. The companyʼs focus was the launch of a new automated vinyl window production line at its Zambrow (PL) site. This production line has been producing the new P-Line window system since January 2018, setting new standards for window production in Poland. The new window system will enable Dobroplast to increase its revenue in Germany and other western European markets, while at the same time expanding its presence in the mid and upper price segments in Poland. The companyʼs brand profile and logo also underwent a makeover.
Despite intense competition in 2017, Slovaktual was able to enhance its role as market leader in Slovakia, thanks to its strong sales presence. Sales to specialist companies were also increased in the Czech Republic and Austria. However, its withdrawal from the contractor services business in the Czech Republic in order to focus on its specialist trade business turned out to be a lateral development overall. As with EgoKiefer, Slovaktualʼs product range is currently undergoing comprehensive expansion and updates, forming the basis for future revenue growth. At the same time, the division is investing a significant sum in the expansion of its centre of production expertise in Pravenec (SK). For instance, an in-house insulating glass production facility was launched in 2017 and window production capacities were further expanded.
At Wertbau, the focus for 2017 was on the introduction of the new generation of wood/aluminium windows and the ramp-up process at the new centre for production expertise, which went into operation in June. The restructure of production for future capacity expansion had a dampening effect on revenue development. While Wertbau continued to benefit from the large number of new construction projects in Germany through its contractor services business, its business with trade partners suffered from a stagnating renovation market.
Products, technology and innovation
The successful introduction of the new generation of wood/aluminium windows in the German-speaking markets marked the divisionʼs first ever cross-company and cross-market window platform. It will continue to drive forward this integrated approach in future.
In the reporting year, the division developed a pioneering standard vinyl profile platform, which will form the basis for the vinyl and vinyl/aluminium windows, lift-and-slide doors and balcony doors developed by the local sales organisations in future. New vinyl and vinyl/aluminium lift-and-slide doors based on this new 76mm and 88mm profile platform were launched in Switzerland, Austria, Slovakia and the Czech Republic in 2017. The products were very well received by customers, leading to the old 70mm (EgoKiefer) and 85mm (Slovaktual) lift-and-slide doors being withdrawn from the market in early 2018. New window systems based on the platform were presented to customers at the beginning of 2018 and will be available for sale from the second quarter onwards. In addition to outstanding technical results and a wide variety of design options, the designer bevel “Ego®Perfect” is particularly worth highlighting in this regard. Thanks to a new type of welding technology, visible bevels are now a thing of the past for laminated windows.
Along with the launch of the standard profile platforms, the companies have also harmonised their fittings, glazing options and other additional equipment. Using this consistent platform strategy enables the division to meet the highly varied and ever-increasing customer requirements in all target markets without increasing in-house complexity and parts stability to an excessive level. At the same time, this enables the division to combine the forces of all of its companies to simplify in-house processes – from procurement and production to delivery – and, as a result, improve costs, product availability and delivery performance.
Another milestone for 2017 was the launch of the in-house insulating glass production facilities at the Pravenec (SK) site. With a capacity of around 600 000 m² of insulating glass, it will cover over 90% of in-house demand in future. With this development, the range of insulating glass has been massively expanded in order to meet future technical directives in the field of personal safety and protection against falls in Switzerland and Germany.
Sustainability
Sustainability is a major element in the divisionʼs range of services; after all, windows that deliver superior standards of thermal insulation help to ensure that buildings use as few resources as possible for heating and cooling.
At every site, window production is carried out with consideration of the environment and in cutting-edge facilities. For instance, all lacquers used in the four-stage application process on wood windows at the Langenwetzendorf (D) site are water-based. The fully automated coating system allows for the best possible utilisation of the lacquer. A compressor station was installed at the Zambrow (PL) site in 2017 with the aim of recovering heat created during the coextrusion of vinyl profiles. The heat generated is used to heat the halls and thus helps to cut costs even further. Thanks to coextrusion systems installed at both the Pravenec and Zambrow sites, off-cuts from vinyl profiles are now fed back into the production process instead of being thrown away.
However, sustainability also includes the ongoing support and development of employees and business associates. In light of this fact, the Division launched the “EgoKiefer Academy” in 2017. Offering a wide range of training opportunities for the fields of sales, technology, project management, assembly and other relevant areas, the aim of this facility is to reinforce and continuously enhance existing expertise. As well as on-site seminars and training courses, online tutorials are a popular form of teaching, enabling the academy to reach the relevant groups quickly without any travel expenses.
Outlook
2017 saw the implementation of important projects for transforming the division into an integrated European window manufacturer. These created the foundations needed to gain a significant share of the highly competitive European window market over the medium term and achieve above-average profitability.
The ramp-up process for the wood/aluminium window production in Langenwetzendorf (D), as well as the insulating glass production facilities in Pravenec (SK) and the other ongoing change projects will continue to impact on the division in 2018. Due to the positive effects from the measures already implemented, the management assumes that revenue and profitability will increase significantly in 2018. The majority of the transformation is due to be complete by the end of 2018.
Highlights
“EgoKiefer Academy”: On-site experts
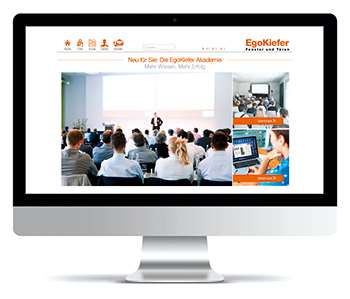
EgoKieferʼs new training concept is helping to ensure that your local contact gets the best training possible. The Academy offers practical training and online tutorials so we can meet the requirements of tomorrow. It also features a brand new image: modern, online and transparent. EgoKiefer – Simply convenient.
Launch of in-house insulating glass production
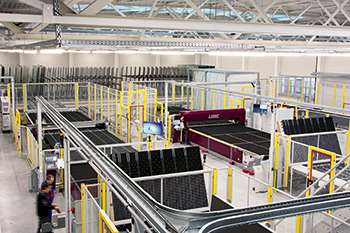
Right on schedule, the first panes of insulating glass ran off the in-house production line in Pravenec (SK) in November. One of the most cutting-edge insulating glass production systems in Europe has been installed in the newly built hall (12 000 m²). By the end of 2018, this system will be able to cover over 90% of in-house demand.
A new benchmark in window production in Poland
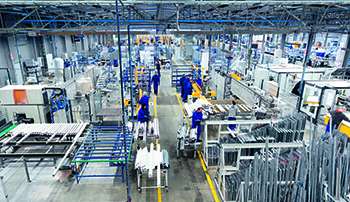
The P-Line window system, which is produced on the new production line, is setting new standards in Poland when it comes to quality, process reliability and automation. A total of 800 windows are produced here every day using a 3-shift model. Along with the brandʼs new image, P-Line will help to significantly increase revenue from high-price segments.
Opening of the centre for wood/aluminium production expertise
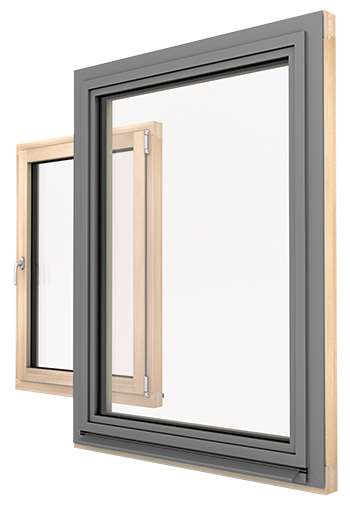
The new wood/aluminium production facilities in Langenwetzendorf (D) launched operations in June. Around 200 000 m² of wood/aluminium windows could be produced here in future. A high level of automation across all stages and RFID control guarantee the highest standards of quality with much lower production times.