Emissions and energy
Article 964a ff. Code of Obligations
Concept and due diligence
All business processes, from research and development to production to logistics and transport, consume energy and cause emissions. Arbonia wants to operate with the lowest possible emissions across its entire value-added chain and aims for a 4.2% average annual reduction in operational CO2 emissions from Scope 1 and 2 by 2035 (compared to the reference year 2020). The greenhouse gas emissions from Scope 3 are now also to be considered in the target, which is why Arbonia has committed itself to short- and long-term emission reductions in accordance with the net zero standard of the SBTi.
The main objective of all companies is to grow responsibly and to aim for maximum energy efficiency. The companies are continually taking new measures to achieve this. The energy efficiency of our production processes is monitored as standard and investigated with regard to optimisation potentials. For this purpose, clear competencies and energy representatives have been designated. These representatives from the areas of development, production, and logistics continuously monitor the target achievement. All targets in the area of energy efficiency are evaluated annually.
Measures including evaluation of effectiveness
Arbonia is steadily increasing the share of renewable energy in its own electricity consumption by expanding the provision of photovoltaic (PV) systems and biomass CHP plants at its production sites. Arbonia continues to work towards more energy efficiency, whether from process optimisations, improvements to machines and technologies, or energy-efficient renovations. While energy management is an important task of all companies, individual companies also have corresponding certifications for energy and environmental management systems. We also increasingly rely on e-mobility. Individual locations have electric vehicles in their fleet as well as electrically operated utility vehicles in use. In addition, electrical charging stations have sometimes been installed for employees and third parties to further support the use of e-mobility.
Material risks and how they are handled (own scope of business and, where applicable, business relationships)
Growing customer expectations regarding sustainability as well as increasing legal requirements entail risks that we are able to counter – both at our own company and in the upstream and downstream parts of the value-added chain – with scientifically substantiated climate targets, an improved data situation, and corresponding measures. A higher quantity of data and an improved quality of data will allow us to provide more detailed information about material risks and how they are handled in future.
Key performance indicators
The key performance indicators include in particular energy consumption according to energy sources (MWh), the composition of energy consumption (MWh), as well as the greenhouse gas emissions of Scope 1–3 (t CO2e).
Emissions in the individual scopes
We focus on consistently reducing the emissions from our own operational processes (Scope 1 and 2) which result from operation, production, transport, and logistics. For this purpose, we rely on renewable energies from PV and biomass CHP plants as well as more energy-efficient processes, machines, and infrastructure. Energetic and environmentally relevant key figures play a significant role in the planning and application of production technology. Greater machine efficiency, preventive maintenance and continuous servicing, optimisation of manufacturing control, and precise planning of downtimes are central to this. In the reporting year, it was possible to achieve an absolute reduction in greenhouse gas emissions from Scope 1 and 2 of 6% compared to the previous year. While the consumption of conventional electricity decreased by 6.6%, the use of renewable electricity also increased by 29.7%.
We are aware that a large part of our total emissions occur in the upstream and downstream value-added chain (Scope 3). To create an in-depth data basis, we systematically recorded our Scope 3 emissions for the first time in 2023. The categories from Scope 3 identified as material include:
- 3.1 Purchased goods and services
- 3.2 Capital goods
- 3.3 Upstream fuel- and energy-related emissions
- 3.4 Transport (upstream)
- 3.5 Waste
- 3.7 Employee commuting
- 3.9 Transport and distribution (downstream)
The Scope 3 emissions increased in individual categories compared to the last reporting year. In the case of purchased goods and services, an increase can be attributed on the one hand to the higher purchasing and production volumes of some companies. On the other hand, the data collection was refined and expanded in 2024. This also applies to the category of capital goods, while individual companies were able to collect considerably more comprehensive data on additional investment types. While some companies were able to reduce their emissions in upstream transport, these emissions increased at other companies due to increased purchasing volumes. In addition, Kermi was dependent on a new supplier that delivers from a considerably more distant location, causing transport-related emissions to increase.
As a result of the expansion of data collection and more precise methods of calculating the Scope 3 emissions, Arbonia is able to present a more comprehensive and more realistic picture of the emissions along its value-added chain. The data collection is being continuously expanded in respect to quality as well as quantity, in order to serve as the basis for defining science- based targets and measures for emission reduction in Scope 3 in the future.
Key environmental figures
1 Direct emissions due to the production of the greenhouse gases methane and nitrous oxide, which are not absorbed during growth. Biogenic CO2 emissions emissions are reported outside of scopes according to the GHG protocol and amounted to 31 341 t CO2e in 2024 and 33 406 t CO2e in 2023.
2 For Scope 3.1, 3.2, 3.4, 3.5, 3.9: headquarters in Arbon, Interwand, Joro and are not part of the scope, as their contribution to Arbonia’s total emissions is estimated to be negligible due to their small size and activity.
3 Refers to production-related products from Tier 1 suppliers.
4 Refers to machinery, equipment, buildings and vehicles from Tier 1 suppliers with a value of CHF / EUR > 10000.–.
5 Refers to the transport of the goods considered in Scope 3.1.
6 Refers to the waste of the goods considered in Scope 3.1.
7 The calculation is based on an employee survey on commuter behaviour from 2022.
8 Transport of the products sold and marketed to customers. Storage is excluded.
Data and calculation basis
The calculation of the greenhouse gas inventory follows the guidelines of the WRI / WBCSD Greenhouse Gas Protocol.
Scope 1: Emissions from fuels.
Scope 2: Emissions that result from the production of purchased electricity. Country-specific emission factors are used here ("location-based approach").
Scope 3: The categories 3.1. Purchased goods and services; 3.2. Capital goods; 3.3.Upstream fuel- and energy-related emissions; 3.4. Transport (upstream); 3.5. Waste; 3.7. Employee commuting, as well as 3.9. Transport and distribution (downstream) are reported in accordance with the Greenhouse Gas Protocol. Country-specific emission factors are also used here ("location-based approach").
Emission factors used: IEA (2023), DESNZ (2023), US EPA (2023), and Ecoinvent 3.11.
Measures for greater climate protection at the companies
One measure for more energy efficiency is certification according to ISO 50001. This international standard requires a complete monitoring of energy key figures, among other things. Arbonia Glassysteme, Garant, Kermi, and Prüm have such energy management systems. To reduce further environmental impacts, Kermi and RWD Schlatter have established an environmental management system in accordance with ISO 14001 and have themselves correspondingly audited regularly.
Energy efficiency is an important factor especially in the modernisation of production lines and peripheral systems because it allows significant reductions in power consumption. The degree of self-sufficiency is also continually increased through the construction of new energy generation systems or the expansion of existing ones. Attention is also paid to energy-saving technology in new buildings and renovations at the operating sites.
For example, Garant replaced fluorescent tubes in the dispatch and storage area with LED lighting in 2024 and is planning such a replacement in the production area for doors and frames in 2025. Heat quantity measurement was used to identify potentials for waste heat utilisation, such as refrigeration from waste heat using absorption cooling, the renovation of air-conditioning systems, or the supply of waste heat for neighbouring commercial customers. In addition, Garant succeeded in continually reducing the energy demand of the production by retrofitting the equipment and optimising the compressed air generation. In 2021, Garant began planning a state-of-the-art biomass CHP plant, which will be commissioned in 2025. This plant will cover around 50% of the power requirements of the production plant. The commissioning of this new plant will eliminate the need for liquid gas as a heating energy source and further reduce the use of heating oil. This also reduces the indirect CO2 emissions of Garant due to the transport of waste wood as well as its disposal and transport costs.
In the reporting year, Prüm concentrated on improvements to plant efficiency and successively starting up new plants. The heat and power generation of the biomass CHP plant entailed numerous challenges; the plant was unable to reach its capacity due to technical problems. As a result, an extensive boiler conversion became necessary in autumn 2024, after which it was possible to put the plant back into operation shortly before the end of the year. With this basis, the share of power and heat generation from own production waste is to be considerably increased in 2025. The electricity production only covered 2 x of the in-house power requirements in the reporting year. On production-free days, the electricity was fed into the grid. In the reporting year, heat was generated with the old biomass combined heat and power system, and excess was used to supply a nearby company.
At Invado, selected employees in the production processes went through a training course during the reporting year to improve the efficiency and effectiveness of the machine utilisation and the material flow. The objective is increase the flow and production efficiency with the same machines. In addition, two new high-speed doors were installed to reduce the opening cycle in winter; further replacement measures are planned for 2025. Furthermore, Invado replaced approx. 610 m2 of a hall roof for better energy efficiency.
Kermi also completed a roof replacement with a new insulation on over. 15,000 m2 in the reporting year. Further energy-saving measures include the continued changeover to LED lighting, the use of motion detectors over approx. 10,000 m2 as well as the optimisation of installation runtime. At Kermi, hall windows, doors, and production plants were also checked for possible energy losses and optimised where necessary. In the powder coating plant, the resource utilisation was optimised through heat recovery and optimised pump control; in addition, a more efficient exhaust air routing was tested.
A central project at Arbonia Glassysteme in the reporting year was the new procurement of a pre-composite furnace for producing laminated safety glass (LSG), which already led to power savings of 197 MWh and thus 75 tonnes of CO2. This savings corresponds to the total annual per person greenhouse gas emissions of almost 5.7 Swiss people. In addition, the exhaust air of an LSG furnace is modified in a production hall to utilise the waste heat better and reduce the heating oil consumption. It was possible to start the constructional and heating adaptations in 2024.
At the TPO company, a new compressor with lower energy consumption was purchased in 2024. Due to fire damage, oil was used for heating at TPO in the reporting year; however, work was started on installing a new heating system for burning wood or wood materials from manufacturing. The goal is to obtain 100% of heat from these materials in the future.
In the first year, RWD Schlatter generated 310 MWh for their own consumption and supply to the electricity grid with their PV system at the logistics centre in Roggwil (CH), which roughly corresponds to the annual electricity consumption of 62 Swiss households. The existing PV system is also to be expanded as part of the roof renovation planned for 2025. In addition, various measures for optimisation and increased efficiency were implemented at RWD Schlatter. One example is improvements to the compressed air preparation, which allows approx. 55 MWh to be saved per year. For 2025, a heat exchanger is planned for the compressor, so that waste heat generated during compressed air preparation can be used and supplied to other processes, such as for example the painting line. In the reporting year, it was also possible to lower the temperature for drying the adhesive by 25% and shorten the pressing time, which leads to further energy savings. Parallel to this, work was begun on expanding the existing control system in order to control energy flows such as heating, cooling, or process heat as needed and continuously optimise them.
Interwand was recorded for the first time with this report. Their PV system, which was already commissioned in 2014, produces approx. 140 MWh per year, of which 80 MWh are fed into the grid and compensated. The biomass system, which has also existed since 2014, has a 550 kW boiler output, the heat of which is exclusively used for their own operation. Around 10% of the biomass originates from their own wood waste.
Optimisation measures are under way in procurement at all production sites of Arbonia to ensure that collection and return transport arrangements are made with as many suppliers as possible in order to avoid empty trips. The progressive digitisation throughout Arbonia, which is becoming increasingly relevant to logistics, allows more energy-efficient logistics together with consolidation of the route planning by optimising routes, bundling travel, and avoiding unnecessary trips. For example, deliveries at Kermi are optimally utilised with their own lorries, and return transports for other companies are enabled for a fee. Comprehensive planning tools play a central role here. This helps to avoid emissions.
Strengthening biodiversity
Arbonia is implementing concrete measures and is driving innovations to minimise the negative impact on biodiversity. With regard to the use of chemicals, the companies continue to increasingly rely on water-based coating materials instead of solvents. As a further example, Prüm is optimising the use of resources in the painting process by using the so-called overspray efficiently. The excess paint is collected and reused, which can reduce paint consumption by around 29%. Prüm has also contributed to preserving biodiversity by renaturing a compensation area of 12 567 m² several years ago and guarantees the financing of the required maintenance of the deciduous mixed forest until 2050. Invado cooperates systematically with the local community to support the planting of trees along the local streets. In the reporting year, Garant planted over 1 000 trees in total through an internal tree-planting action and a further one in cooperation with a school from Erfurt.
Consistently monitored objectives
At the companies with a certified energy management system in accordance with ISO 50001, the monitoring has led to a greater sensitivity for energy savings. At Kermi, for example, measurements are regularly taken in production via a state-of-the-art data acquisition system to identify any weak points and immediately replace inefficient consumers. At Prüm, approximately 100 in-plant energy measurement points are in operation for the machines and the infrastructure. Arbonia Glassysteme calls up all consumptions in real time with a state-of-the-art energy management system. An automated reporting system makes it possible to take countermeasures when defined limit values are exceeded. Prüm and Garant each have an energy team which is responsible for the current status and initiates improvements. At Invado, the energy consumption in the entire company as well as in the individual production halls is also regularly monitored and compared with the figures for the previous year. Invado also participates in the Enel X Demand Side Response programme for limiting output, i.e., a temporary reduction of the electricity consumption upon request by the transmission system operator. Audits are additionally carried out at regular intervals. RWD Schlatter also has an energy management system, where targeted measures are continually derived from the energy key figures that are collected and analysed monthly.
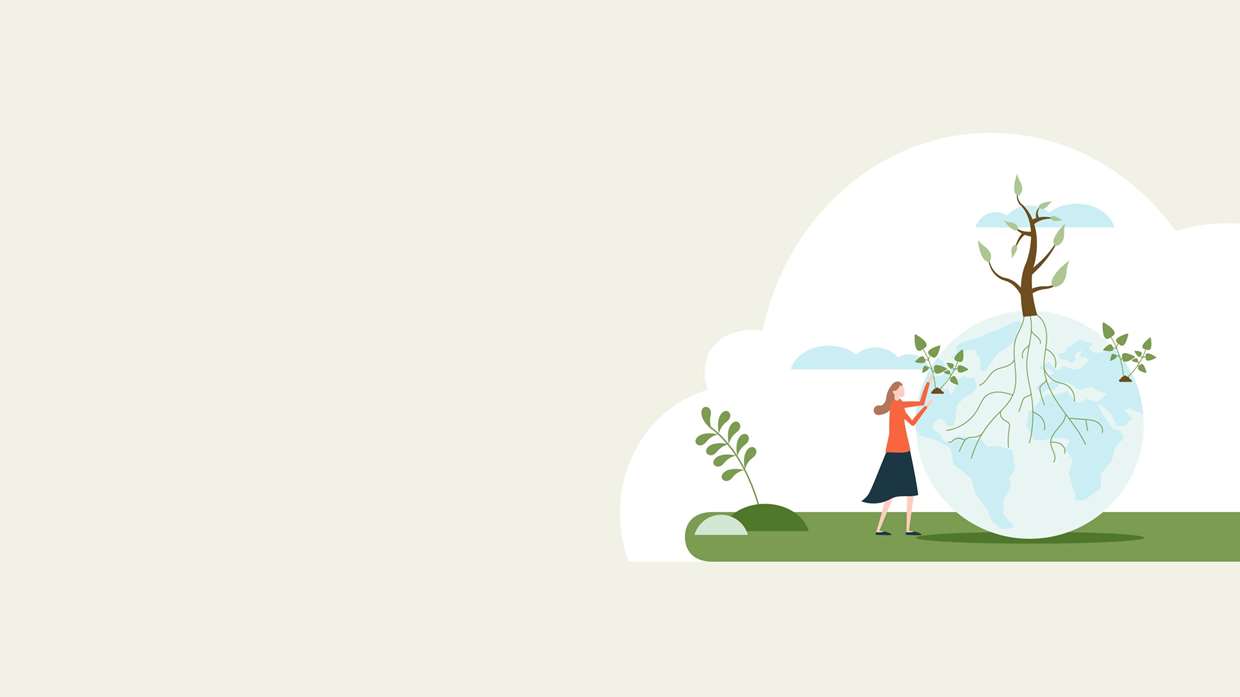