Use of resources and circular economy
Article 964a ff. Code of Obligations
Concept and due diligence
Our objective is to conserve natural resources and to encourage a materials cycle that is as circular as possible. This saves expenses for the transport and preparation of raw materials and thus energy in this process as well, which also supports our energy efficiency goals. Various functions at the company share responsibility for the cross-sectional issue of resource management. Product Management and Development have the task of designing products that can be produced in as resource-efficient a manner as possible. The production managers are responsible for ensuring that processes are designed with resource efficiency and a circular economy in mind. A waste policy has been in place throughout Arbonia since the 2022 financial year. This provides a guideline for the consistent separation of operational waste, stipulates that production must be reviewed with regard to resource-efficient processes, and requires that the waste volume must be measured.
Measures including evaluation of effectiveness
Arbonia has established a foresighted resource management system, focusing on high quality and production that is as free of defects as possible in order to prevent rejects and complaints. Energy and material savings are to be taken into consideration when developing new products and improving existing ones. Usable production waste or old parts are used again in manufacturing where possible. In 2024, the respective companies were able to increase the share of recycled materials and reduce plastics in products and packaging. The use and expansion of digital systems supports resource-efficient operations at Arbonia.
Material risks and how they are handled (own scope of business and, where applicable, business relationships)
Market distortions and supply chain problems can cause raw material prices, other material prices, and freight prices to rise. Further risks are products and services that are difficult to obtain or unavailable. The higher manufacturing costs of our products cannot be passed onto the customers in full or quickly enough, which can lead to additional costs, delivery delays, revenue decreases, and loss of margins.
Key performance indicators
The key performance indicators for us include the key figures relating to error costs, waste according to disposal method, and water consumption.
Priority for resource conservation
Arbonia wants to conserve natural resources. For this purpose, we rely on a foresighted resource management to save material as well as energy. This is supported by digital solutions for planning and tracking production processes and is continually improved. Resource savings are central to the development of new products as well as the improvement of existing products, whereby the use of old or common parts is also checked. A production that is as error-free as possible saves resources. For this reason, reject and error costs are continuously monitored and corresponding improvements are initiated. In the reporting year, our error rate increased slightly, which was due to the replacement of machines at Prüm, among other things. Corresponding countermeasures have been started to reduce the rate in the future.
The companies continually check where resources can be conserved. In the case of packaging materials, for example, the companies are changing over to materials made from renewable raw materials such as cardboard and paper wherever possible and increasingly eliminating plastic or polystyrene. Kermi, for example, has changed over the complete packaging of their showers to cardboard without plastic foil. Packaging wood is being successively changed over to honeycomb panels with high stability. The measure to continually reduce the share of Styrofoam, which was begun in 2023, was continued but not fully completed. At RWD Schlatter, residual material from Sonitus mid-layers is used as an intermediate layer for transport. Invado has set itself the goal of delivering doors and frames exclusively in cardboard packaging in the future. The replacement of Styrofoam with cardboard as corner protection was 90% achieved in 2024 and is to be implemented 100% in 2025. In addition, the foil thickness is to be reduced, which will lead to around 20% less material use. Interwand plans to introduce an automatic beam processing centre that could save more than 10% of the scrap and thus allow 7000 kg less aluminium to be used per year.
It was not possible to achieve the goal of reducing water consumption by 10% during this year; we are therefore focusing all the more on targeted measures in order to realise further savings in the future. For example, digital solutions can support resource savings. At Prüm, for example, water consumption recording was integrated in the Efficio program and automated. In this way, irregular deviations, for example, due to leaky water lines, can be quickly detected and corrected even outside of the monthly evaluation. Additionally, a new spraying robot with a cyclone separator was commissioned in 2024, which reduces the water consumption of this plant. Furthermore, Prüm has introduced a new serial door leaf press which enables continuous bonding of the mid-layer panels. This makes it possible to avoid material scraps, which lowers resource consumption and reduces the amount of production waste.
With the objective of saving material, paint consumption tests are continuously being carried out at Garant as well. In addition, it was possible to change over from paints containing solvents to more environmentally friendly water-based paints in the reporting year. Furthermore, the material thickness of the protective boards used for transport support was reduced, and this weight savings leads to fewer emissions. At Garant as well, work was begun to further expand Efficio in the area of energy data collection (electricity, compressed air). The components of water and heat are to be added to it in the coming years in order to enable a precise analysis of the consumption values. The introduction of SAP and the resulting database will make it possible to create a consumption forecast with optimisation and savings potentials.
We were able to achieve further optimisations through digitisation with exhibitions and sample exhibits. Digital 3D POE systems ("point of experience") are increasingly being used there. As a result, savings can be achieved in the production, transport, and assembly of sample elements, while clients receive a more precise product selection, which in turn reduces re-orders and corrections. In the Wood Solutions Business Unit, over 100 POEs are already in use, which can be used to show over 1 million product combinations at a scale of 1:1 in high-resolution 4K image quality. Bekon-Koralle also shows the different product variants with a digital system at their location.
Waste management
In addition to resource savings, Arbonia strives to keep reusable materials in circulation as long as possible. For example, in the Glass Solutions Business Unit, all showers with suspected damage are inspected and resold if possible if the quality allows it. Otherwise, all valuable parts are disassembled and reused. A decrease in waste and the related direct and indirect costs pursued in general. We measure the waste quantities and analyse the error costs in order to assess the effectiveness of the measures. The waste resulting at the company is consistently separated, pretreated where necessary, and recycled when possible. The quantity of products that are disposed of through waste incineration and sent to landfills is also to be analysed and minimised.
At Bekon-Koralle, for example, no products are sent to waste incineration or landfills. The products (shower enclosures) consist of glass, aluminium, and metal parts. All these materials are collected and handed over to a nearby recycling company. Complete shower stalls from returns are sorted for their individual materials at the recycling centre.
Dust and shavings that are generated in production at Invado are partly incinerated in a specially prepared furnace, while the energy is used for warm water and heating buildings. Other waste such as plastics, metals etc. are recycled. Small quantities of hazardous waste are picked up by a company with a corresponding approval. All waste that leaves the Invado production plant is registered in the state-run database BDO, which enables evaluations and subsequent optimisations to reduce waste.
Prüm also relies on digital support for waste management; the solution here developed in-house also offers comprehensive evaluation possibilities via a cloud-based recording.
RWD Schlatter reorganised the waste management in the reporting year and centralised it for the first time, which makes the disposal process more efficient, minimises transport routes, and allows further improvements.
In addition, Interwand has established an internal circular economy, in which packaging materials are returned from the construction site and reused for new orders as much as possible. So far, 80% of the materials can be reused. There is also a waste concept according to which all waste materials are collected by type and recycled.
Key water consumption values
Key figures for resource efficiency
The figures for commercial and hazardous waste cover all manufacturing companies in Arbonia as well as the headquarters in Arbon, Switzerland. Pure distribution companies were not included.
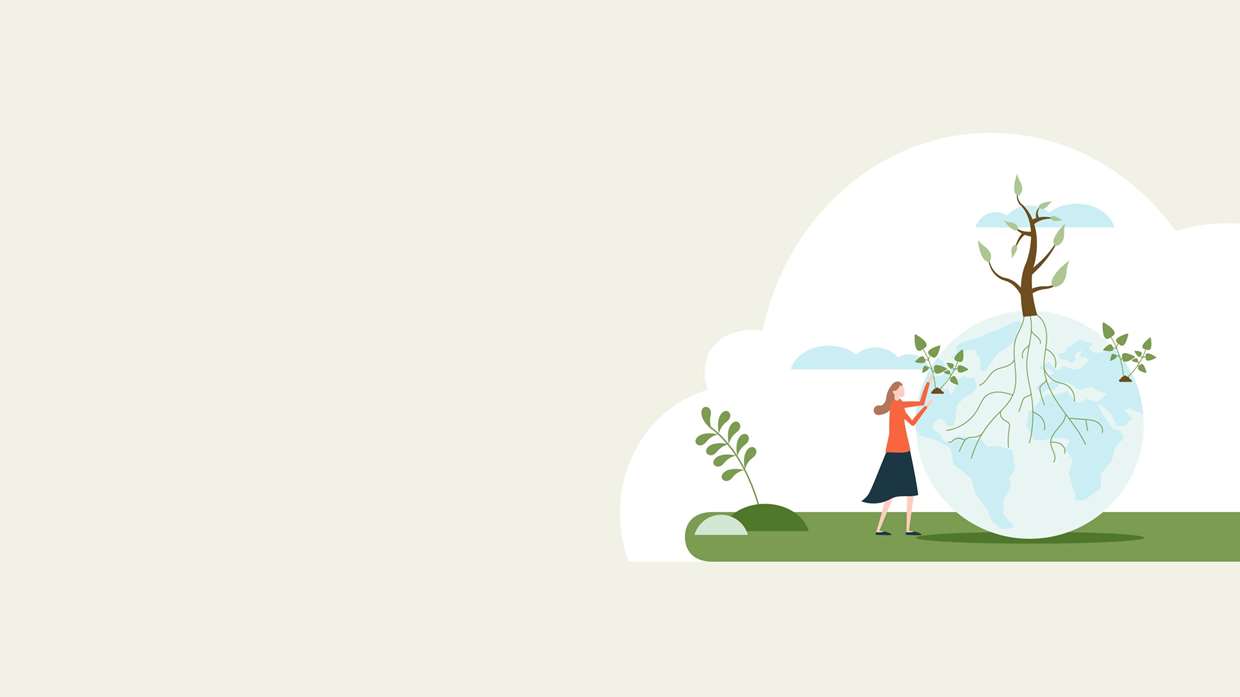