Occupational health and safety
Article 964a ff. Code of Obligations
Concept and due diligence
Our concept for occupational health and safety is based on a three-pillar concept. The first pillar contains measures for prevention, and the second pillar absence management, which concerns interventions. The third pillar contains case management, which promotes integration or re-integration. All three pillars are supported and developed together with the relevant stakeholders – Group Management, managers, HR employees, business partners, as well as social partners. The production managers, managing directors, HR managers, and the works council are responsible for occupational health and safety. In addition to this, specific people are designated as responsible within the individual companies.
Measures including evaluation of effectiveness
Risk avoidance and health protection are central topics in all employee training at Arbonia. We continually analyse the processes internally and externally; for example, through special workplace inspections together with the responsible people. Furthermore, Arbonia annually invests in labour-saving machines such as, for example, lifting systems. If accidents occur, they are immediately analysed, and measures are initiated to minimise the risk of accidents. To avoid and identify health risks to employees early on, we hold leadership courses for supervisors on a regular basis. Employees can take advantage of professional company medical care as well as preventative medical check-ups. During this reporting year as well, we expanded the health management system and took specific measures to minimise non-occupational accidents further as well. These include courses for stress management, first aid courses, and psychological support services. The measures are aligned with the needs of the workforce via corresponding employee surveys.
Material risks and how they are handled (own scope of business and, where applicable, business relationships)
Consistent occupational safety is also an important topic for us due to its impact on the operating activities of the companies: Every accident and downtime causes additional costs. The consequences can be production delays or downtimes, as well as reputational damage and lower work morale.
Key performance indicators
The key performance indicators for occupational health and safety are the proportion of employees covered by an appropriate management system, the absence rate, the accident frequency rate, the accident severity rate, and the number of deaths.
Safety and security as a priority
As Arbonia, we want to ensure a health and safety culture at a high level by operating safe production plants as well as sales locations. This involves the prevention of accidents and injuries, continuous risk analysis with derived measures, as well as proactive heath promotion in the workplace.
The aim is to lower absences, prevent illnesses, and reduce mental and physical stress. All of our sites fulfil the legal regulations for the respective countries, which means that we could in principle apply for certification according to OHS AS 18001 or ISO 45001. So far this has not been necessary due to the high legal as well as social partnership standards at our locations.
Various committees of the companies (occupational safety committee, health working group, works council committee, occupational health and safety protection) hold regular meetings to analyse the current situation and develop suitable measures. Arbonia also promises its customers in every work contract to maintain the highest standards in respect to occupational safety. External business partners who work on the business premises of Arbonia apply the same safety rules.
Key figures for occupational health and safety
¹ The survey method was changed at several companies in 2023, which is why the key figures are not comparable in relation to 2022.
Health promotion, prevention, and training
Arbonia offers company health programmes. Examples include the "Focus on People" platform of the Glass Solutions Business Unit and a comprehensive range of courses and training. Employees can additionally take advantage of professional company medical care as well as preventative medical check-ups. All employees of Arbonia have access to subsidised, occupational health services and health promotion programmes such as fitness, yoga, and Pilates. Health problems such as back pain are actively prevented with ergonomic workplaces.
In 2024, Invado completed a social audit at one of its customers with a positive result. Invado also passed the annually carried out sanitary-epidemiological station visits with a good result. To reduce physical strain on employees, Invado continues to work on automating the production process. For example, in the reporting year, Invado installed a new door frame assembly machine that works fully automatically and produces less noise than the predecessor model. In addition, a robot station has automatically placed the doors on pallets since 2024, which considerably reduces the strain on employees. A system for folding and gluing cardboard edges fully automatically has been set up, because the changeover from polystyrene edge protection to cardboard edge protection has required employees to manually fold and glue the cut cardboard sheets until now. The machine now performs the entire process automatically.
Automation solutions of this kind were implemented at the other companies some ago, taking the strain off employees and increasing effectiveness.
RWD Schlatter has its own health management system which is looked after by a five-person health panel. Current topics are discussed on a regular basis in collaboration with those responsible for Arbonia’s company health management scheme and measures are initiated as appropriate. In the reporting year, various measures were carried out by the health panel. It offered discounts on herbal remedies to strengthen the body’s defences as well as ear protection for employees in production and organised a first aid course as well as a fire extinguishing course. In addition, there was a campaign for flu vaccinations again. The illness rate as a result of occupational and non-occupational accidents was also analysed.
In addition to the usual instructions for occupational health and safety for people joining the company, Bekon-Koralle created a three-year plan for preventing non-occupational accidents together with the SUVA (Swiss National Accident Insurance Fund). Furthermore, all employees completed a course on the topic of "household and DIY" in the reporting year. "Tripping / falling" is scheduled for the following year.
In Germany, Kermi implemented several measures for noise reduction as well as for ergonomic improvements in the reporting period. For example, new work stations in production are height-adjustable, exoskeletons provide support when lifting or carrying, and at the new assembly lines, lifting and carrying are completely eliminated.
Interwand has procured a new lifting system for transferring glass, which replaces the previous manual work. It allows physically careful as well as more efficient working, which has considerably increased employee satisfaction.
At Arbonia Glassysteme, a test of the use of an exoskeleton in production started during the reporting period. In addition, employees are trained to be safety officers. In 2024, the employers’ liability association was on site for a consultation appointment regarding occupational safety, and this occasion was used to evaluate further measures.
The Garant company introduced fire-fighting and first aid training as well as company health management. Furthermore, operational procedures were optimised to replace cutting tools with tools that have improved, integrated safety measures. In cooperation with the health insurance companies, back screenings were carried out in the reporting year, and measures to quit smoking are planned for 2025. In addition, a day on the topic of health was organised for 2025.
Continually reviewed targets
In addition to internal reviews, Arbonia also relies on regular feedback from external agencies to help achieve its targets. In 2024, for example, Garant received positive feedback from the employers’ liability association BGHM for its efforts to decrease reportable accidents and the positive development of the company in the area of hazard assessments and correspondingly derived measures. In general, Arbonia receives important feedback for such improvements through area inspections by the industrial inspectorate and trade unions as well as from external safety audits. Regular inspections of the work conditions and machines take place in respect to occupational safety, in which work environment tests (e. g. noise, weights), medical examinations, and risk assessments are carried out at the workplace. In addition, the employees continually go through safety training.
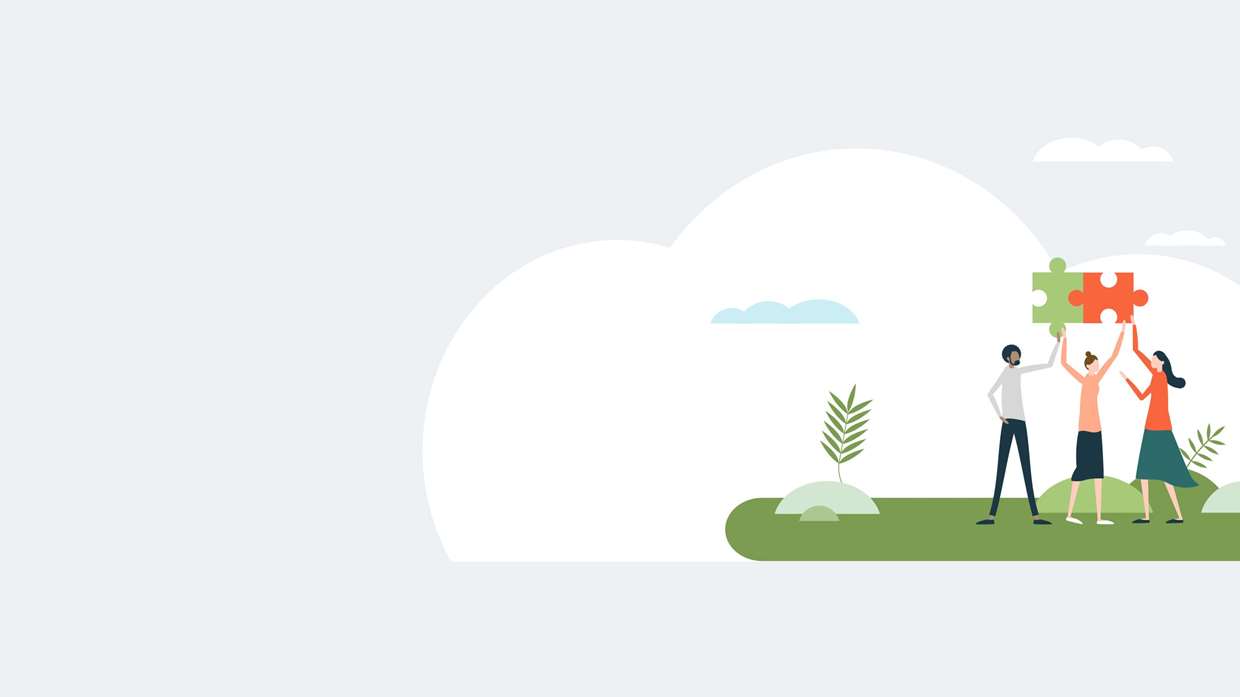