CO2 and energy
The issue of "CO2 and energy" is important to Arbonia in two ways: A great potential for reducing greenhouse gases is found in buildings, which are the largest cause of CO2 emissions in Europe after mobility, with a share of over 30%. There is therefore a high demand for products that reduce the energy consumption in buildings and ensure a pleasant indoor climate at the same time. Arbonia recognized this trend early on and makes a substantial contribution with its products. Improvements can be achieved with new buildings as well as with renovations – especially through the use of integrated system solutions, but also through the use of individual components of the HVAC Division. Furthermore, the interior doors made of wood and glass help to reduce the energy consumption of buildings thanks to their insulation.
At the same time, Arbonia wants to manage with as few emissions as possible in its own operations, in production, and in the area of transport and logistics. In the reporting year, the Group has defined a reduction path for its own CO2 emissions (Scope 1 and 2) on the basis of the Science Based Targets Initiative and defined corresponding targets and measures. Arbonia is aware that the emissions of the upstream and downstream value added chain (Scope 3) are likely to be a large part of all emissions. It is therefore in the process of identifying the largest influencing factors for the Scope 3 emissions, in order to formulate reduction goals and measures for this as well.
In the reporting year, Arbonia already succeeded in increasing the share of renewable energy in total energy consumption to 41.0% (previous year: 38.1%). The 15% increase in the company's own electricity production through the expansion of photovoltaic systems significantly contributed to this. As a result of this and the increased use of renewable electricity, Arbonia was able to increase the share of renewable energy in the total electricity consumption from 23.6% to 32.7%. A further success was the 18.7% reduction in heating oil consumption for heat generation. On the whole, Arbonia has succeeded in reducing its GHG intensity (greenhouse gas emissions in kgCO2e/CHF net revenue) by 11.2% despite a considerably higher productivity.
In addition, Arbonia is planning to publish its environmental data in accordance with the Carbon Disclosure Project (CDP) in 2022. The commitment in the area of CO2 and energy is beneficial to Arbonia because it allows the company to meet the increasing customer expectations concerning sustainability as well as growing legal requirements.
Key environmental figures
1 The company's own electricity is produced by means of photovoltaic systems and a wind turbine. These plants do not cause any CO2 emissions during operation.
2 Direct emissions due to the production of the greenhouse gases methane and nitrous oxide, which are not absorbed during growth. Biogenic CO2 emissions are reported outside of scopes according to the GHG protocol and amounted to 34 782 t CO2e in 2021 and 34 417 t CO2e in 2020.
Data and calculation basis
The key environmental figures include the resource consumption of all manufacturing companies of the Arbonia Group as well as the headquarters in Arbon (CH). Pure distribution companies were not included due to their comparatively low environmental impact. The calculation of the greenhouse gas inventory follows the guidelines of the WRI / WBCSD Greenhouse Gas Protocol.
Scope 1: Emissions from combustibles and fuels.
Scope 2: Country-specific emission factors are used ("location-based approach"). Emission factors used: IEA 2020 and DEFRA.
Heating, Ventilation and Air Conditioning Division
Better environmental balance for company and customers
Environmentally related activities affect all business processes – from research and development to production up to logistics and transport. It is correspondingly important that a contribution to reducing greenhouse gas emissions and saving energy is made at every level. The HVAC Division has paid special attention to these topics for many years and is continually taking new measures to improve the environmental balance further. A consistent reduction of energy consumption and CO2 emissions not only makes an important contribution to protecting the environment and resources – it can also improve economic efficiency and the market position as a result. The topic of energy efficiency, which is important for optimising production, is naturally also considered in advance when developing new products: In this way, the HVAC Division ensures that the environmental balance of the customers is also improved by energy-saving products.
Saving energy – and producing it ourselves
The HVAC Division has been dealing with the topic of energy efficiency for many years – at the latest since various production sites were certified according to the strict ISO standards 14001 and 50001, which demand continuous monitoring of the energy key figures, among other things. Monitoring and assessment of the energy efficiency within the division are therefore standard – as is a systematic procedure that is ensured by clear responsibilities and the company's own energy officers. These officers from the areas of production and logistics ensure that the goals in the energy area are met. As in the past years, the energy management has concentrated on the largest consumers: With further investments in modern production plants and energy-saving LED lighting, it has been possible to reduce the electricity consumption. For example, Sabiana has optimised the electricity consumption for the new coating line. Thanks to the installation of LED lights in the halls SAB 2 and 3, it has been possible to reduce the annual energy consumption by 130,000 kW/h. The new plant also has a lower gas consumption.
At the same time, the division has increased the electricity generation with its own photovoltaic systems, so that more and more sites can produce a large part of their electricity requirement themselves. The company's own wind power turbine with an output of 2 megawatts at the Vasco site Dilsen (BE) as well as the installation of low-temperature heating/cooling equipment that was carried out in the reporting year at Vasco as well also help to optimise the energy balance. Kermi has also continued the targeted optimisation of the entire vehicle fleet in Plattling (D) according to the emission standard "Euro 6", which will reduce the CO2 emission of the division by at least 400 tonnes per year. The division is also systematically pursuing the strategy adopted to construct an integrated, CO2-free system for an efficient and energy-conscious generation, transfer, and storage of heat. For example, Kermi will be investing in a highly efficient, gas-operated CHP plant at the Plattling (D) site in 2022, which will lead to CO2 savings in the amount of at least 425 tonnes annually. In Czech Opočno and Stříbro, state-of-the-art energy standards are taken into account in the new construction of a new heat pump production plant and in the investment in new compressors. The reduction of energy consumption is analysed and monitored at these sites in the framework of Six Sigma projects, a management system for process improvement.
Ambitious goals – impressive successes
The manufacture of energy-efficient products requires energy. The HVAC Division has the goal of reducing this energy and increasingly obtaining it from renewable sources. The reduction of energy consumption and the expansion of energy supply from renewable sources aim to improve the CO2 footprint considerably. Furthermore, the continuously optimised bundling of loads and the resulting decrease in the number of necessary trucks should reduce transport costs. In addition, the division uses telematics data to check and optimise the driving behaviour and routes. Vehicles with high emissions are replaced by new ones, for example, at Sabiana.
In addition to the implementation of the photovoltaic system, the renovation of the welding line cooling as well as the heat recovery in the welding fume extraction in the steel panel radiator production at the large site of Plattling (D) led to a considerable reduction in energy consumption in the reporting year.
Provision of green areas at local sites
The preservation of biological diversity is closed linked to commitment in the area of CO2 and energy. After an analysis of the biodiversity at the Plattling (D) site, initial measures were taken to protect and strengthen flora and fauna. The creation of green spaces and the planting of additional trees on the company premises will promote biodiversity at the local sites of the division. In addition to green areas, the supply of innovative and efficient products and the associated production and marketing processes also play a decisive role in promoting biodiversity. The division therefore places value on manufacturing on existing or reduced areas, despite volume growth in the sense of production consolidation. Areas with dense building structures in the production plant are offset with biologically cultivated compensation areas.
Implementation of the strategy with consistent monitoring
Because higher energy efficiency and reduced CO2 emission are strategic goals of the HVAC Division, the corresponding measures are checked with a continuous monitoring of the key figures in energy management. This also makes it possible to measure the proportion of regenerative energy in the individual companies of the division. The main goal of all companies is to grow responsibly and strive for maximum energy efficiency.
Doors Division
Responsibility for reducing CO2 emissions and energy consumption
Previously untapped potentials for increasing the energy efficiency and reducing the CO2 emission can be more quickly and more easily identified with a holistic view of the topic. It is a fact that optimising the energy consumption – along with improving the CO2 balance – has long since become a task of all companies, departments, and areas of the Doors Division. Specifically, every person has the possibility of pursuing this goal and making their own contributions in the form of suggestions for improvement. All goals in the area of energy efficiency are defined annually and underscored by corresponding actions in the Doors Division.
Numerous measures for greater environmental protection
The measures for increased efficiency are checked and ensured through consistent energy management. An annual budget is available for measures for increased efficiency. Furthermore, some of the companies regularly perform certification audits according to the standards ISO 9001, 14001, and 50001. Energy efficiency is an important factor especially in modernising production lines and peripheral systems because it can reduce electricity consumption. Planned or already implemented investments in state-of-the-art production facilities, as well as the consistent use of energy-saving LED lighting, continually reduce the electricity consumption in the companies of the Doors Division. Garant, for example, set a goal in the reporting year to reduce its energy consumption by 100,000 kWh per year by upgrading the lighting to LEDs. Energy-saving technology is of course also used for new buildings and renovations at the operating sites. And finally, the degree of self-supply is continually increased further by constructing new energy supply systems or expanding existing ones. At the door production plant of Prüm, residual materials from manufacturing are used for heat and electricity production: The 30-year-old CHP plant there is currently being replaced by a new plant due to new environmental protection regulations. The new CHP plant, which will go into operation in 2023, can produce twice as much electricity from biomass waste as the old plant. As a result, Prüm will be able to produce up to 60% of its electricity requirements from its own generation . The Garant production plant will be taking a similar path: In 2021 the planning phase was started there for a state-of-the-art CHP plant that will go into operation in 2024. This plant will similarly cover around 50% of the electricity required by the production plant.
Conservation of biodiversity
One of the most important direct drivers for the loss of biodiversity are climate changes due to the release of greenhouse gases resulting from fossil fuel consumption. The Doors Division therefore implements concrete measures and innovations to protect biodiversity. It has reduced the total solvent emissions for the manufacture of doors by one third in the past years and now relies more on water-based coating materials. The Prüm company has helped to restore a compensation area of 12,567 m² and guarantees the financial support for the necessary maintenance of the deciduous mixed forest for the next 30 years. Most recently, the division has dedicated itself to creating beehives and bee colonies as part of its wood training workshop.
Consistently monitored goals
The Doors Division wants to reduce its own footprint even more in the coming years by reducing its energy consumption and generating its own energy from renewable sources to the greatest possible extent. In addition, not only manufacturing facilities are optimised for increased efficiency but also production processes – such as, for example, with the introduction of a shopfloor management at RWD Schlatter in Switzerland. At Invado in Poland, the electric power consumption could already be decreased thanks to continuous modernisation of the production facilities. To achieve a maximum effect, the infrastructure components that had a high energy consumption or a high failure rate were replaced first. With further optimisation of the production lines, the use of a monitoring system for electricity consumption, and the replacement of lighting in the production halls, the energy consumption as well as the CO2 emissions per manufactured product are to be reduced further in the coming years. Specifically, the meta-halogen light sources are to be replaced by energy-saving LED lights at Invado. At the Prüm site, it has been possible to lower the energy consumption per manufactured part to 10.95 kWh – considerably below the target value defined in 2020 – through higher machine productivity, the changeover to LED lighting, and the continuous use of energy-saving motors. At Kermi Sanitär in Platting (D), it was also possible to reduce the energy consumption through a changeover to LED lighting and shopfloor management, among other things. At this site, the consumption is monitored via installed meters.
The cross-divisional energy management systems made it possible to considerably simplify the analysis of consumption values, leading to a higher sensitivity for energy savings. At Kermi and Bekon-Koralle, for example, measurements are carried out in production via a modern data acquisition system at least once a month – sometimes even daily – to identify any weak points and immediately replace inefficient consumers. Prüm and Garant ascertain monthly specified energy performance values and have their energy management systems externally checked and certified every year (TÜV and ICG). At Prüm and Garant, the energy and environmental management is also evaluated as part of the yearly management review. The current consumption during operation is also regularly monitored at Invado in Poland and compared with the figures for the previous year. To check the efficiency of the measures taken, the energy consumption as well as the CO2 emission is determined for each manufactured product. In addition, audits are carried out at regular intervals. RWD Schlatter also has energy management: Targeted measures are derived from the energy key figures that are collected and analysed at least once a year.
Progress and successes
At Kermi and Bekon-Koralle, a cross-functional team of the Glass Solutions Business Unit has developed a new concept for reducing packaging material: To reduce transport weight – and thus improve the environmental balance – the previous wooden packages were replaced by equally functional but considerably lighter cardboard honeycomb panels. At the Garant production plant, a comprehensive energetic evaluation of the manufacturing facilities and the associated infrastructure was introduced in 2021. The corresponding results are analysed by the energy team every month so that management can intervene immediately if variances should occur. In the reporting year, the company was able to fill the position advertised for the areas of energy and environmental management with an expert, thus achieving an important step in continually improving its sustainability performance. The future CHP plant at the Prüm site is currently in the implementation phase and will be fully operational at the beginning of 2023. The new plant will cover approx. 60% of the entire electricity requirement of the door production plant and additionally heat an area of around 24,000 m². It will be a challenge to keep the energy efficiency ratio at a low level because the future frame production plant of Prüm will require a great deal of electricity during the construction and start-up phase – without producing a corresponding amount of parts.
The use of a new CNC machine at RWD Schlatter led to an increase in efficiency and a reduction in energy consumption in production. The installation and commissioning of the new plant was carried out despite problems from temporary border closings due to the COVID-19 pandemic. Invado also successfully passed an inspection of the Polish environmental protection agency. In the middle of the year, a new edge plant from Homag was also put into operation that reduces rejects thanks to increased production quality. In combination with increased efficiency, this circumstance has a positive effect on the energy consumption per manufactured product.
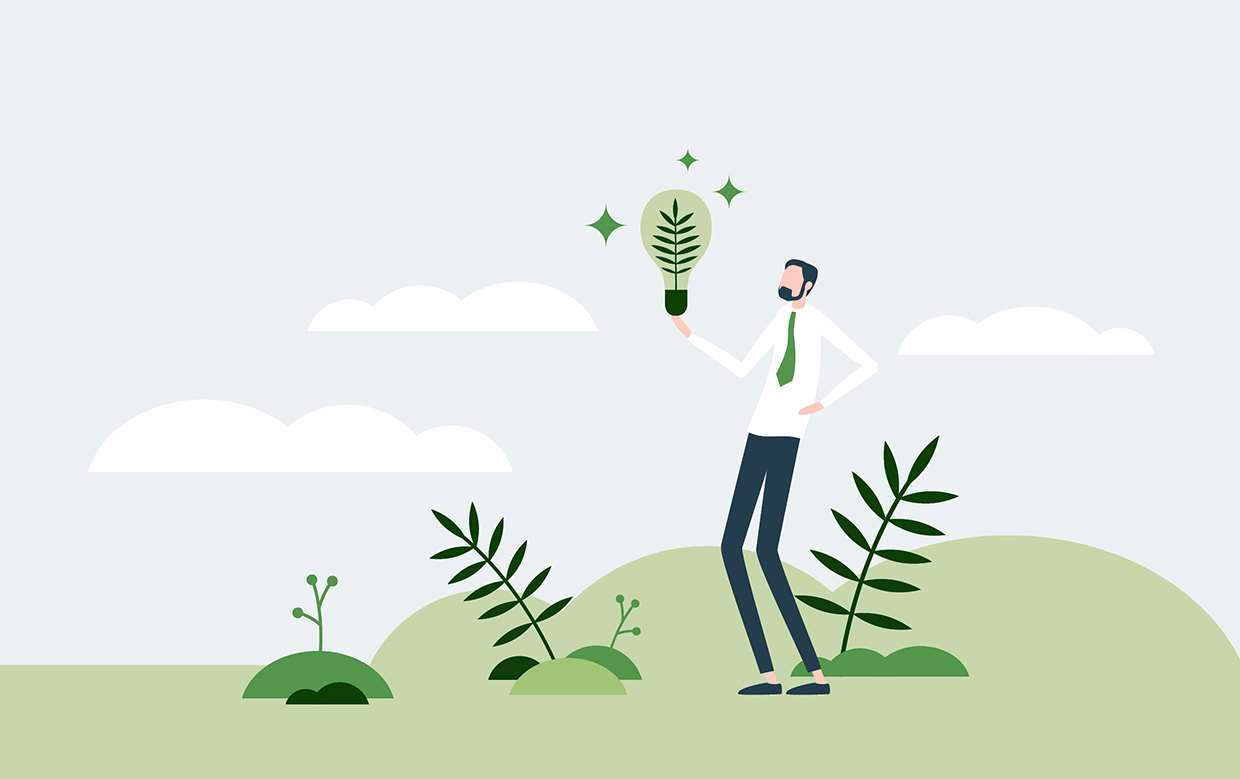