- Occupational health and safety
- Heating, Ventilation and Air Conditioning Division
- Doors Division
- Safety has top priority
Occupational health and safety
Arbonia promotes a culture of safety and health at a high level by operating safe production plants as well as distribution and logistics sites. Avoiding accidents and injuries is just as much a part of occupational health and safety as a corresponding risk analysis, derived measures, and a health-promoting work environment. This is to reduce absences, prevent illness, and reduce physical and psychological stresses. Risk avoidance and health protection are a central topic in employee training at Arbonia; Arbonia continually analyses the corresponding developments internally and externally.
The topics of work and health protection are precious assets for the two divisions of Arbonia and their companies. All sites of Arbonia fulfil the related legal requirements of the respective countries, but there is no certification according to OHSAS 18001 or ISO 45001.
During the ongoing COVID-19 pandemic, the health and safety of employees is a priority topic. All subsidiaries of Arbonia quickly took measures to comprehensively protect the employees in the production plants as well as in the offices. Thanks to targeted prevention and regular, free tests, it was possible to maintain regular operation everywhere at all sites in 2021 as well. At many Arbonia sites, employees were able to receive a coordinated vaccination offer.
During the reporting year, Arbonia further expanded the company health management system and took targeted measures to minimise non-occupational accidents as well. Safety training takes place depending on the risk profile of the workplaces. For prevention and early detection of health risks of employees, Arbonia regularly holds leadership courses for superiors.
Key figures of occupational health and safety
The key figures for occupational health and safety cover the employees of all manufacturing companies of the Arbonia Group as well as the headquarters in Arbon, Switzerland. Pure distribution companies were not included. No comparative value is reported for 2020 because the survey method was changed.
Heating, Ventilation and Air Conditioning Division
Motivation and productivity thanks to high safety standards
Since health protection and workplace safety directly help to increase employee satisfaction and improve productivity, these topics are of decisive importance to all areas of the HVAC Division. According to this principle, the air quality in offices is just as reliably monitored as measures for increasing safety in the production area. To prevent accidents and injuries, the responsible people of the division regularly evaluate the safety of the production facilities as well as all measures for improving this safety. The same holds true for the risk analysis of the company and the correspondingly derived action plan. Further measures for promoting health and safety are the continuous analysis of the exposure of employees to hazardous substances, an inspection plan for determining risks and improvements, as well as regular safety training. Consistent occupational health and safety is also an important topic for the HVAC Division because of its effects on the operating activities of the companies: Every accident and downtime causes additional costs. Risks involve a slowdown or failures in production, loss of reputation, and negative effects on employee morale.
The HVAC Division succeeded in reducing the days lost due to work accidents by 10% compared to 2020 through targeted measures for increasing work safety.
Prevention thanks to training and process optimisation
All employees of the HVAC Division receive annual safety and fire protection instruction matched to the needs of their work area. Internal and external safety training courses are regularly offered by the division – training to be a first aider and company paramedic every year, for example. In addition, all relevant training courses of their labour unions are also open to the employees.
Every accident report is tracked by an occupational safety officer in the individual companies. It is checked whether similar accidents can be avoided in the future by changing the procedures or by additional safety measures. The Sabiana company is currently introducing an occupational safety management system according to the international standard ISO 45001 that is based on the already implemented and certified quality management system ISO 9001.
Employees are provided with the protective equipment and work safety clothing required for their work free of charge, and each employee receives safety instructions for their workplace. In addition, defibrillators are available at all locations. If accidents or illness should occur, shift paramedics and first aiders are available.
Less absence – higher employee satisfaction
The main goal of the HVAC Division in the area of occupational safety is to promote and maintain the health of all employees. In addition, effort is made to reduce the accident and illness rate and to establish a consistent health and safety culture. This specifically concerns risk identification in all areas of the company as well as measures for reducing these risks and for eliminating potential hazard sources. Further topics are the optimisation of physically strenuous tasks as well as making employees aware of the topics of accident prevention, occupational safety, and health promotion. At all companies, statistics concerning the sickness rate and the accident rate give a monthly overview of the current situation. The low absence rate and the high productivity prove that the HVAC Division is well positioned in respect to health and occupational safety.
A variety of measures – despite COVID-19
With the "Job Bike" initiative, the HVAC Division gave the employees at the Plattling (D) site access to e-bikes in 2021 as well. Numerous employees took up this offer in order to do part of their personal fitness programme on their way to work and thereby improve their own quality of life and health. At Kermi, a possibility for smoking cessation was offered via the Health Task Force (in a virtual format due to the ongoing COVID-19 pandemic). As a result of the pandemic, no seminars, courses, or lectures on occupational safety could be held in the reporting year. Preventative medical check-ups (e.g. skin cancer screening) were also cancelled due to contact restrictions. After the measures due to COVID-19 are repealed, Kermi intends to make these offers available to all employees again. At Sabiana, it was possible to continue the programme for improving machine safety according to the targets.
Doors Division
Safety has top priority
For the Doors Division, avoiding accidents and injuries is just as much a part of occupational health and safety as a corresponding risk analysis. A safe and healthy work environment is made possible by regular safety tours with all parties and corresponding improvement measures. The activities in the area of occupational health and safety include raising the awareness of employees, risk assessment at the workplace, ensuring machine safety, as well as the prevention of accidents and occupational illnesses.
Health promotion, prevention, and training
Occupational health and safety are central and decisive topics in the entire value-added chain of the division. The reasons for this are obvious: Increased safety and prevention can prevent injuries and illnesses – and sometimes even save lives. At the same time, a clear commitment to occupational safety can also improve operational processes and profitability as well as reduce the risk of liability: Healthy, effective employees are the basis for optimised processes with less inactive time and higher product quality.
Because the safety and health of employees always have top priority for the Doors Division, the lowest possible accident and illness rate is aimed for. The individual companies take numerous measures to maintain and promote the health and performance of the employees. This includes, among other things, company health programmes such as the platform "Focus on People" at Kermi and Bekon-Koralle or an extensive range of courses and seminars on a variety of topics. Professional company medical care and preventative medical check-ups can also be taken advantage of.
To identify possible hazards early on, the different committees of the companies (work protection committee, health task force, works council task force, work and health protection) hold regular meetings to analyse the current situation and develop suitable measures. Internal area inspections and hazard analyses have been implemented for all workplaces as a cross-divisional standard. Standardised processes make it possible to avoid hazards as much as possible. At Prüm, Garant, and Invado, specific employee instructions on safety issues are already the norm. At RWD Schlatter, occupational health and safety is part of quality management; it is continually developed further by the safety officers and the shop floor management. In every work contract, the company also commits to its customers to maintain the highest standards of occupational health and safety. External business partners who work on the business premises of the division also commit to observing the previously communicated safety regulations of the division.
All employees of the Doors Division have access to subsidised occupational health services and programmes for health promotion, such as fitness, yoga, or Pilates. The division also provides each production employee with an individually adapted hearing protection. Health problems such as back pain are actively addressed by optimising the ergonomics at the workplace. Newly hired employees receive an in-depth safety instruction for their workplace and are trained for the requirements in their work area in regular courses.
Invado plans to install an automatic unloading unit for stud doors, in order to avoid manual unloading of heavy material in the future. A door buffer station is also being set up behind the machining centre to eliminate the hard manual work in this area. At the other companies, such automation was already implemented a long time ago – which has led to great relief and increased effectiveness.
Continually checked targets
Invado has set itself the goal of offering a comprehensive occupational safety training not only for newly hired employees but also for the technical and administrative employees as well as managers. Specific training courses are to be increasingly offered for technical staff. To achieve these goals, the company is also relying on the regular feedback of external parties, in addition to internal reviews. Examples of this are area inspections by the factory inspectorate and labour unions as well as external safety audits.
At Kermi and Bekon-Koralle, the monthly statistics on sickness and accident rates provide an overview of the current situation and serve management as a tool for optimising occupational safety. In addition, the causes of each accident are carefully analysed. This concept has proven to be extremely successful – absences due to accident or illness only occur seldomly at the two companies. Motivation and loyalty to the employer are correspondingly high.
At Garant, Prüm, RWD Schlatter, and Invado, the current situation regarding occupational safety is also continuously checked and assessed. At Invado, this check also includes the analysis of the results of work environment tests (e.g. noise, weights) and medical examinations as well as the performance of risk assessments at the workplace. Occupational safety is increased further by continuously monitoring the working conditions and the machine efficiency as well as continuous safety training of the employees.
A year characterised by COVID-19
As a result of the ongoing pandemic, no seminars, courses, or lectures on occupational safety and health-promoting activities could be held at Kermi and Bekon-Koralle. The magazine "Focus on People" was cancelled along with the preventative medical check-ups offered in the previous years. As soon as the COVID-19 measures are repealed, these offers are to be started up again. There will also be more prevention offers and lectures from the health task force again.
At Invado, all courses also had to be held online due to the COVID-19 pandemic. The work system of the company was adjusted according to the COVID-19 regulations: Fewer people and greater distances in the offices as well as the provision of masks and disinfectants allowed safe working with a reduced risk of infection. The department for occupational safety and fire protection additionally launched various measures for improving occupational safety conditions. All employees have the possibility to express wishes, complaints, and comments on this.
Employees are consistently involved in the design of the occupational safety systems because they have valuable suggestions for improvement. At Kermi, all work processes are regularly checked – with the aim of minimising physically demanding or strenuous activities through technical support or the use of machines. In the administrative area, the individual work situation is continuously optimised thanks to regular area inspections by the company doctors – for example, through the use of height-adjustable desks. At Sabiana, internal area inspections and hazard analyses are standard for all workplaces. Employees benefit from a health insurance that provides preventative medical check-ups for the entire family.
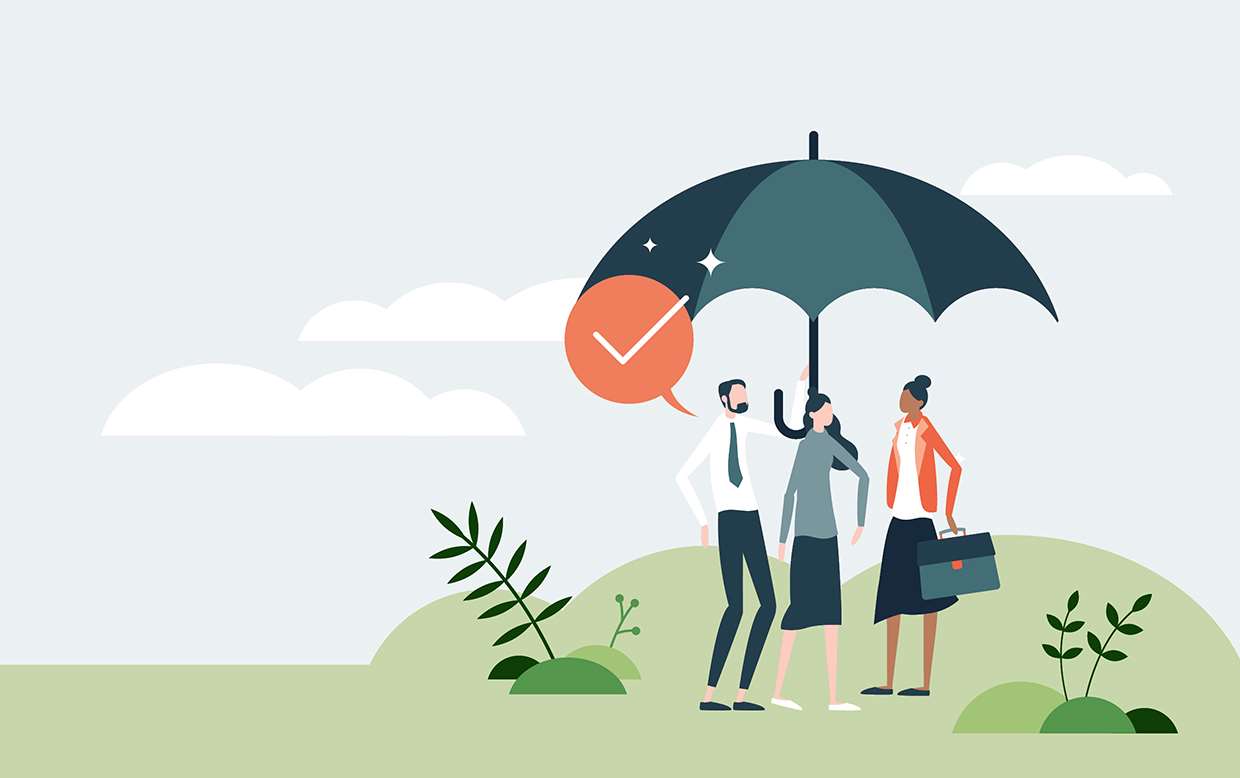