Digitisation
Digitisation is understood to be the conversion of analogue processes and work steps into digital formats and the storage of information in digital systems. At Arbonia, for example, cooperation at construction sites is simplified thanks to increasing digitisation – such as through Building Information Modelling (BIM) and Product Information Management (PIM). These and other digital processes eliminate sources of error and reduce the manual effort for employees. The direct access to information and services, as well as simpler processes and faster processing times, are increasingly expected by customers, partners, and employees. In this way, digitisation offers a possibility to stand out among competitors. Since the beginning of 2021, the divisions have been responsible for the digitisation process again. They let themselves be guided by the users' requirements when implementing the corresponding projects. Agile working methods and lean management principles are applied here. The digitisation process is already showing an impact: Customers, partners, and employees are becoming increasingly aware of Arbonia's digital competencies.
Heating, Ventilation and Air Conditioning Division
Efficiency thanks to digitisation
The companies of the HVAC Division understand digitisation as the use of new technical possibilities to further develop their own business and processes and to make them even more efficient. Digitisation is essential to the division because it makes it possible to work faster and more accurately as well as to use the time gained for activities with added value. At the HVAC Division, digitisation is the topic that affects business activity the most, apart from decarbonisation. For example, the company achieves a consistently automated handling process for each order through the consistent use of all relevant SAP modules.
Digitisation as a competitive factor
For the HVAC Division, digitisation is relevant throughout the entire value-added chain – from development to production and logistics up to administration. Basically, all processes can be digitised and thereby improved. Digitisation can not only support internal processes but also make the individual companies more competitive and more attractive. In manufacturing digitisation is consistently advanced – for example, through the increasing networking of the production plants via the control room technology. Industry 4.0 and Logistics 4.0 lead to a considerably increased efficiency and reduced use of resources in production and logistics. Digitisation also has a great relevance in product development, because the products are increasingly being linked within the division to improve energy efficiency further.
Processes are also being increasingly digitised and automated in administration and sales. At Kermi, for example, classic sales is gradually developing into multi-channel sales. The use of social media and the development of proprietary product apps is just as natural for the company as the use of the Intranet as a comprehensive information platform. At Sabiana, a new role has been coordinating the cooperation of the IT department with projects to increase the digitisation in production and administration since 2019. The corresponding progress is checked semi-annually.
Digital in development and production
A concrete digitisation project in the area of development is, for example, the market launch of a new energy store for photovoltaic systems with an integrated energy management system (EMS) at Kermi: With networking of all components, the EMS allows the generated electricity to be optimally used. The system ensures that as much as possible of the self-generated electricity is used in one's own household and as little as possible has to be purchased. At Sabiana, one of the main goals of digitisation is the internal configuration and implementation of the new Manufacturing Execution System (MES) in the entire production and the implementation of the Computerized Maintenance Management System (CMMS). Further goals are the introduction of a new production process control (digital kanban) to reduce inventories, the introduction of a warehouse management system (WMS), as well as the introduction of a new production planner and a code configurator. At Vasco, an upgrade of the ERP system has been started; the go-live is planned for June 2022. Afterwards, the company wants to devote itself to implementing artificial intelligence (AI) and robotic process automation (RPA) while continually increasing the security in the area of information and communication technology at the same time. The desired objectives are checked with regular feedback from the stakeholders, comparisons with competitors, and a semi-annual assessment.
Networking in products and production
At Kermi, the networking of system components proceeded in the reporting year as planned. The expansion of knowledge in the area of new technologies is a challenge that can be managed well, however, thanks to intensive cooperation with colleges, institutes, and specialised companies. In the reporting year, Sabiana was able to realise the installation of 70 digital workplaces and a new Manufacturing Execution System (MES) in production.
Doors Division
Harmonisation of the digitisation roadmap
In addition to the comprehensive investment programmes in the modern production plants, the Doors Division is also focusing on the topic of digitisation. This holds many opportunities, such as making work processes easier and reducing errors through automation. In 2019, the Wood Solutions Business Unit initiated a digitisation roadmap, along which it has since substantially renewed the existing IT landscape to make the systems ready for the future.
The core of this IT strategy is the introduction of SAP S / 4 Hana as a modern and harmonised ERP system for the entire business unit and the related automation of the core business processes – from paper to digital. The changeover to this uniform "foundation" allows the division to create a solid basis for future growth and for further digitisation projects. An important advantage of this uniform system is that additions and new products only have to be developed once instead of individually for each company of the Wood Solutions Business Unit (e.g. MES for production, web shop etc.). In the reporting year, the division intensively advanced the changeover of the system landscape of Invado in Poland, which will take place in the first step, followed by the other companies of the business unit.
Linking of machines and processes
In the course of the SAP introduction, Invado started introducing a system for operating and machine data acquisition (MES) in the reporting year; this will ensure a seamless linking of machines and business processes and thus increased efficiency. In addition, the existing web shop of Invado will be replaced with a new, more modern solution that is directly connected to the new SAP system, reducing internal effort.
Efficient door calculation tool
With the planned introduction of DoorIT, the Prüm and Garant companies will completely digitise their offer process for customers in the future. This is a web-based door calculation tool that is supplied with the most current figures and information. This will markedly reduce error rates and time expenditure for the customers as well as for the companies.
Digital twin
RWD Schlatter is working on a new solution to drive its own digitisation and to increase customer loyalty in the maintenance business in particular. The planned solution will allow customers to view the options and the state of their doors online. They also have access to all documents at all times. In this way, information on opening and closing cycles, moisture, vibrations, and temperature can be read to determine the ideal maintenance time. In addition, the customer can directly trigger a report to the maintenance team via a QR code at the door. All relevant data are available to the corresponding contact people at RWD Schlatter at all times. This saves time, since time-consuming queries and clarifications are no longer necessary. Thanks to this solution, RWD Schlatter helps to make its customers' everyday life easier while the company also optimises its internal processes.
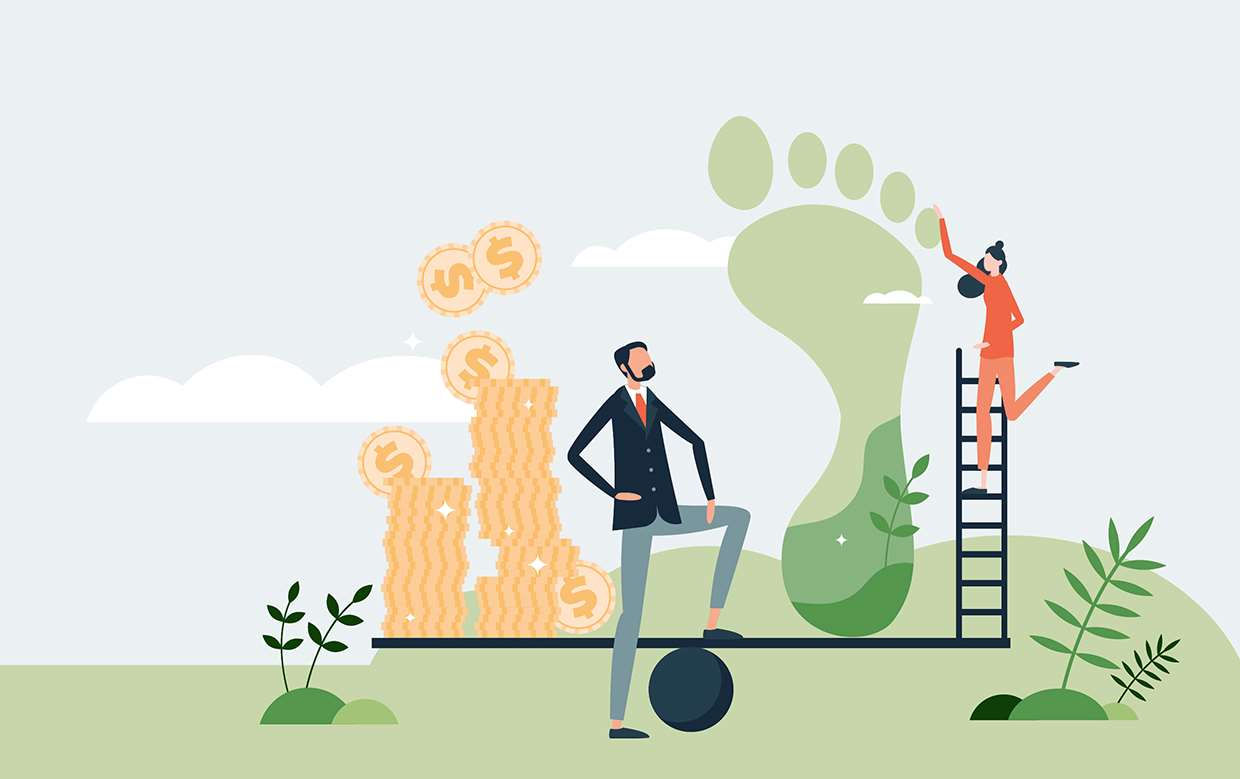