Product management
In addition to the product responsibility including quality assurance, product management also comprises product labelling. This includes all communication and marketing services concerning the individual products as well as the corresponding certifications. Product management is the interface from the company to the market and identifies changes to customer requirements and the legal framework. These changed requirements are implemented in the development. The responsibility of product management includes observing valid regulations and standards regarding product compliance, safety and health for (end) customers, as well as dealing with problematic components such as chemicals. A large portion of Arbonia's production sites operate with certifications for environmental management (ISO 14001) and energy (ISO 50001).
Key product management figures
1 Production costs of goods produced at the site, excluding purchases.
Heating, Ventilation and Air Conditioning Division
Interface to the market
As the interface between the individual companies and the market, product management identifies changes in customer requirements so that they can already be taken into account during development. Special attention is also paid to the legal framework: With a strict observance of regulations and certifications, product management is the basis for demonstrating the technical conformity of all products. Standards and regulations for building products are continually becoming more extensive and more demanding. It is a correspondingly great challenge for the product management of the HVAC Division to implement new and existing demands with innovative products. To guarantee this, the division is active in various bodies – such as in the German Institute for Standardisation (DIN) and the Federation of German Heating Industry (BDH). These partnerships make it possible to help shape technical progress and incorporate innovations into product management early on. For this purpose, the processes and product range planning are continually adapted in the HVAC Division, and the responsible employees are trained for new trends and standards as early as possible. Adapted and newly developed products also have to be documented, certified, and protected by patents. For a positive perception on the market, however, aesthetic aspects are also considered in the product design to supplement the sustainably positive effects from use. To increase public interest, selected innovations are presented in the context of design competitions.
Increasing trend of energy efficiency
Kermi was able to introduce the radiator "x-flair" in the reporting year. This supports the use of heat pumps: The flow temperature of the heating system is reduced to an efficient level for heat pumps, which considerably simplifies the use of this technology – especially in existing buildings. In the quest for better environmental compatibility, identifying trends in the European regulations for climate policy – especially in regard to future-capable refrigerants and energy sources – remains the greatest challenge, despite the involvement in various bodies and organisations. One of the steps that Sabiana took in 2021 despite the uncertainties was to advance the development of control and monitoring systems with the goal of optimising the use and the energy consumption of installed equipment and devices.
Products with maximum customer value
The goal of all companies of the HVAC Division is for all products to meet current and future customer requirements as well as existing standards and laws. The division is already making a significant contribution to reducing CO2 emissions in the building sector today with innovative products and system solutions. In addition, it also continues to advocate for achieving the desired climate neutrality: The division strives for a CO2 reduction of 1 million tonnes through the use of its own products in the market by 2025. The division also takes into account other environmental aspects of its products, for example, the groundwater neutrality of decomposition products in the case of damage. At all companies of the HVAC Division, the product development follows a systematic process with defined milestones. In this context, the sales development of new products and feedback from the market environment allow a reliable success monitoring. These new products as well as most other products of the HVAC Division are subject to product certification with the quality marks RAL and NF for radiators, EHPA approval for heat pumps, and DIN Certco approval for underfloor heating pipes. Fan coils have multiple Eurovent certifications, while chimneys have the IMQ certificate.
Guaranteed product safety
Upon delivery of the products, customers receive assembly instructions with corresponding safety information on use, assembly, and maintenance. The customer service of the HVAC Division is also available via a hotline and e-mail. For electrical work, customer service employees of the HVAC Division attend a training course that qualifies them for work on electrical equipment for corresponding assembly. The division has optimised the processes specifically for the heat pump product, which requires ad hoc service, to provide immediate assistance to customers: In the first step, the back office provides 1st level support. If the problem cannot be solved here, the office-based technical support takes over in the 2nd level and checks the heat pump via remote maintenance – up to 70% of the problems can be solved in this way. In the 3rd level, a customer service technician is commissioned to check the system on site or, alternatively, support is provided by a specialist in the technical department.
Doors Division
Product management as a success factor
In light of the increasingly extensive and demanding regulations and standards for building products, a comprehensive product management has long since become essential. The relevance of this area is correspondingly high for the Doors Division as well. The internal product management makes sure that even highly specialised customer requirements are met in every detail and all legal regulations and common standards are observed without compromise by manufacturing in conformity with approvals. In this way, the sales volume of certified products can be successively increased.
Safeguarding product quality is ensured in the Doors Division with the quality management system ISO 9001. In this framework, quality assurance checks the materials used in manufacturing, oversees the production control, and checks the manufactured parts. Guaranteeing the highest quality standards – the core of the standard EN ISO 9001 – makes it possible to maximise customer satisfaction. The building products manufactured by the Doors Division are subsequently placed on the market according to the relevant legal regulations and relevant standards. This requires an in-house production control; the corresponding documentation is ensured by the individual companies in the respective department for quality assurance.
The Doors Division also provides its customers with assembly instructions, training courses, and a customer service in order to guarantee safe handling of the products.
Outstanding quality with maximum conformity
Through active participation in various bodies and through the division-wide exchange of know-how and experience, the companies of the Doors Division are able to help shape technical progress considerably and incorporate innovations early on. This ensures that customers always receive innovative, high-quality, and long-lasting products. The shower stalls of Kermi and Bekon-Koralle, for example, are characterised by exceptional durability. The products are tested according to the strict standards EN 14428 (CE) and PPP 53005 (TÜV / GS) and are therefore characterised by maximum stability, water-tightness, and ease of maintenance. The use of single-pane safety glass up to 10 millimetres thick is documented according to the standard EN 12150.
Garant, Prüm, RWD Schlatter, and Invado also strive for continuous quality improvements: Key factors are the on-going optimisation of quality management and manufacturing processes, the modernisation of machinery, as well as the careful selection of suppliers with the highest quality standards. To motivate employees to take even more responsibility for the quality of products, the Doors Division offers corresponding training courses.
The operations of Invado in Poland and RWD Schlatter in Switzerland are certified according to the ISO standard 9001: Standardised processes not only guarantee the quality of the products but also the delivery reliability and correct product labelling. Well-known certificates for wood from sustainable forestry, testing for harmful substances by the ECO Institute, the Environmental Product Declaration (EPD), and the RAL quality mark of the German Institute for Quality Assurance are further seals of approval for the companies of the Doors Division.
Product safety and suitability for everyday use are the overarching goals for product management at the Doors Division. As a consequence, these two points are continuously monitored – for example, by the internal control system and quality management. The in-house production controls of the individual companies are verified annually as part of external audits. Invado, for example, was successfully recertified in the operating year according to the standard ISO 9001. The standard EN 14351-2, which has still not been harmonised, proved to be a challenge, however. In addition, there are still no clear regulations for product labelling in application of the EU regulation 2019 / 515.
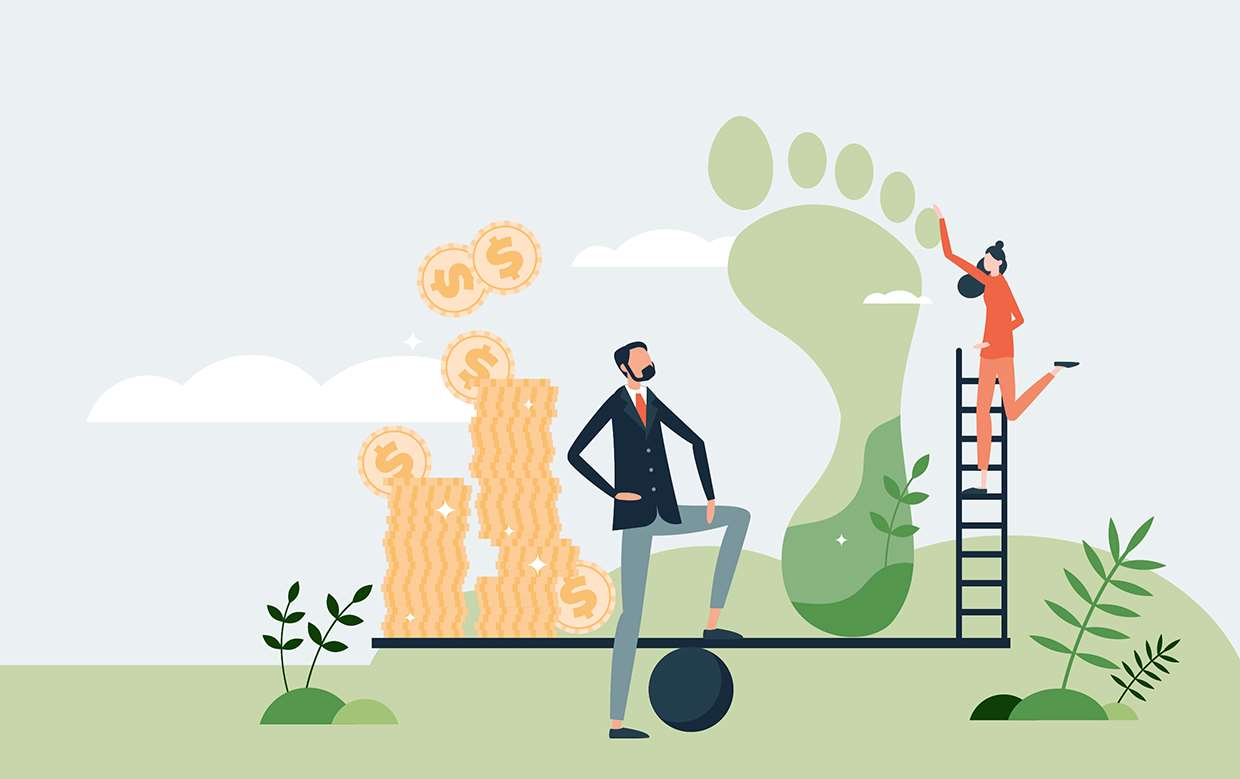