CO2 and energy
The topic of "CO2 and energy" is important to Arbonia in two respects: With a share of over 30%, buildings have a great potential for reducing greenhouse gases; they are the largest source of CO2 emissions in Europe after mobility. Accordingly, there is a great demand for products that reduce the energy consumption in buildings and ensure a pleasant indoor climate at the same time. Arbonia identified this trend early on and makes a substantial contribution with its products. Improvements can be achieved in new buildings as well as in renovations – especially through the use of integrated system solutions, as well as through the use of individual components from the HVAC Division. Furthermore, the interior doors made of wood and glass also help to lower the energy consumption of buildings thanks to their insulation capacity.
We are also aware that conventional energy generation consumes finite resources that contribute to climate change. At the same time, we aim to operate with the lowest possible emissions at our own company, in production and in the area of transport and logistics. In particular the emissions of the upstream and downstream value-added chain (Scope 3) make up a large part of the overall emissions. Arbonia is therefore in the process of identifying the greatest factors that influence the Scope 3 emissions, in order to formulate reduction targets and measures for this as well. In an initial step, the divisions determined the following categories in a materiality analysis:
- Purchased goods and services
- Capital goods
- Energy-related upstream chain
- Upstream and downstream transport
- Waste
- Commuter traffic
Environment-related activities affect all business processes – from research and development through production to logistics and transport. It is correspondingly important that contributions to reducing greenhouse gas emissions and saving energy are made at each level. As Arbonia, we have been paying special attention to this issue for many years and are continually taking new measures to further improve our environmental impact. The optimisation of energy consumption – and thus the improvement of the CO2 balance – has long since become a task of all companies, departments, and areas. Specifically, everyone has the possibility to work towards this goal and make their own contributions in the form of improvement suggestions. All targets in the area of energy efficiency are defined annually and advanced with corresponding measures.
One decisive measure for more energy efficiency are certifications of various production sites according to the ISO standard 50001, which requires a complete monitoring of energy key figures, among other things. The monitoring and assessment of energy efficiency within Arbonia are therefore standard. For this purpose, clear competencies and in-house energy officers have been designated. These officers from the areas of production and logistics continuously monitor the target achievement.
On the basis of the Science Based Targets Initiative, we have determined a path for reducing our own CO2 emissions (Scope 1 and 2) and defined corresponding targets and measures. We aim for an average annual reduction of 4.2% (incl. growth) by the year 2035 (reference year 2020). Initial measures include increasing the share of electricity from renewable energies by expanding the photovoltaic systems, enlarging the fleet of electric cars, and increasing energy efficiency with new machines. A certified energy and environmental management reviews the target achievement and the effectiveness of the implemented measures.
A complete monitoring of the key figures in energy management is the most important instrument for Arbonia to continue to pursue the strategic targets relating to energy efficiency and CO2 emissions. This also makes it possible to measure the share of renewable energy. The main objective of all companies is to grow responsibly and to aim for maximum energy efficiency.
In the reporting year, Arbonia already succeeded in increasing the share of renewable energy in the total energy consumption to 46.9% (previous year 41.0%). Together with large amounts of green energy, Arbonia was able to increase the overall share of renewable electricity in the total electricity consumption from 32.7% to 43.3%. A further success was the reduction in heating oil consumption for heat production by 24.4%. In total, Arbonia thereby succeeded in reducing its greenhouse gas intensity (greenhouse gas emissions in kgCO2e / CHF net revenue) by 9.1% (Scope 1–2).
Arbonia’s commitment in the area of CO2 and energy benefits the company by enabling it to meet rising customer expectations regarding sustainability as well as increasing legal requirements.
Key environmental figures
¹ The company's own electricity is produced by means of photovoltaic systems and a wind turbine. These plants do not cause any CO2 emissions during operation.
² Direct emissions due to the production of the greenhouse gases methane and nitrous oxide, which are not absorbed during growth. Biogenic CO2 emissions are reported outside of scopes according to the GHG protocol and amounted to 34 616 t CO2e in 2022 and 34 782 t CO2e in 2021.
³ Scope 3 emissions will only be fully calculated for the next reporting year. The calculation of the emissions for the present categories was according to the information from the Arbonia Sustainability Report 2021.
Data and calculation basis
The calculation of the greenhouse gas inventory follows the guidelines of the WRI / WBCSD Greenhouse Gas Protocol.
Scope 1: Emissions from fuels.
Scope 2: Emissions that result from the production of purchased electricity. Country-specific emission factors are used here ("location-based approach").
Scope 3: The categories 3.3 Fuel- and energy-related emissions and 3.7 Employee commuting are reported in accordance with the Greenhouse Gas Protocol. Country-specific emission factors are also used here ("location-based approach").
Used emission factors: EEA 2022, DBEIS, LfU Bavaria, and DEFRA.
Heating, Ventilation and Air Conditioning Division
Saving energy – and producing it ourselves
The HVAC Division is continually expanding its capacities for generating its own electricity and heat from renewable energies. A photovoltaic system at the production site in Kladovo (RS) generates around one third of the site’s own power requirements (114.82 MWh in the reporting year). This share is to increase to 50% through a more efficient network supply. The heat production and cooling take place through heat pumps with higher capacities, so that the need for gas is eliminated entirely. The Corbetta (IT) production site is also continually increasing the share of self-generated electricity. Currently, over half of the power requirements are covered by photovoltaics. Further investments are planned in order to further increase this share. In addition, charging stations for electric cars are being installed.
At the Dilsen (BE) site, a wind power generator with an output of two megawatts provides for an improved energy balance. Additionally, the offices were ecologically renovated in the reporting year. Heat pumps were installed here as well, so that gas is no longer needed to generate heat. Furthermore, a new company policy stipulates that only electric cars may be used starting in 2023.
At the Plattling (D) site, the division put a CHP system into operation in 2022 that will lead to CO2 savings of at least 425 tonnes annually. In Opočno, Czech Republic, the most modern energy standards were taken into account in the new construction of a heat pump plant and in the investment in new compressors (see introductory interview for the chapter). The reduction of the energy consumption is analysed and monitored at these sites in the framework of Six-Sigma projects, a management system for process optimisation.
Improvement of the CO2 footprint as a target
The division wants to decrease travel in logistics by optimally bundling loads together. In addition, the division uses telematics data to review and optimise driving behaviour and driving distances. High-emission vehicles are replaced by new ones, for example, at the Corbetta (IT) site, where the fleet was switched to the "Euro 6" emissions standard.
Provision of green areas at local sites
Maintaining biological diversity is closely connected to engagement in the area of CO2 and energy. After an analysis of the biodiversity at the Plattling (D) site, initial measures were initiated to protect and strengthen the flora and fauna. The creation of green spaces and planting of additional trees on the company premises will promote biodiversity at the local sites of the division.
In addition to greening, efficient production and sales processes also play a decisive role in promoting biodiversity. Despite volume growth, the division is committed to manufacturing in existing or reduced spaces to consolidate production. Intensively built areas in the production plant are compensated for by organically cultivated compensation areas.
Doors Division
Numerous measures for greater environmental protection
The measures of the Doors Division for increasing efficiency are reviewed and ensured by a consistent energy management. At the Deggendorf site, all consumption is called up in real time with a state-of-the-art energy management system. An automated reporting system makes it possible to take countermeasures when defined limit values are exceeded. An annual budget is available for measures to increase efficiency. In addition, a majority of the companies regularly carry out certification audits according to the standards ISO 9001, 14001, and 50001. Energy efficiency is an important factor especially in the modernisation of production lines and peripheral systems because it allows significant reductions in power consumption. Further investments in reducing power consumption concern entrance gates, a planned hall roof with new insulation, as well as a photovoltaic system, LED lighting, and the replacement of a filter system. Of course, attention is also paid to the use of energy-saving technology in new buildings and renovations at the operating sites. In addition, a project for energy efficiency analysis is being carried out from which new measures will be derived.
And the degree of self-sufficiency will ultimately be continually increased through the construction of new or the expansion of existing energy generation systems. At the Prüm doors plant, residual materials from production are used to generate heat and electricity: The 30-year-old CHP system there has reached the end of its life cycle and is currently being replaced by a more modern and more efficient system. The new CHP system, which will be commissioned in 2023, can produce more than double the amount of electricity from biomass waste as the old system. This means that the Weinsheim (D) site will be able to generate up to 60% of the power requirements internally. The Garant production plant in Amt Wachsenburg (D) will take a similar path: In 2021, the planning phase started for a state-of-the-art CHP system, which will commence operations in 2024. Likewise, this system will also cover around 50% of the power requirements of the production plant.
In addition to the above-mentioned objectives, the division is also optimising its production processes – as for example with the implementation of shop floor management at various sites. Furthermore, packaging material will no longer contain any foils whatsoever in the future. This will save 60 t of packaging foil as well as additionally 280 m³ of gas per year by dispensing with a foil shrink machine.
Conservation of biodiversity
The Doors Division is implementing concrete measures and is driving innovations to maintain biological diversity. It has reduced the total solvent emissions for the manufacture of doors by one third in the past ten years, for example, and is now increasingly relying on water-based coating materials. The share of solvents is currently only around 7.4% in this regard. By changing over the painting process, Prüm and Garant have also succeeded in achieving considerable savings in paint consumption. They have reduced the consumption by 18 and 40 tonnes respectively to less than 100 tonnes of paint per year. The Prüm company has contributed to the renaturation of a compensation area of 12 567 m² and guarantees the financial support of the required maintenance of the deciduous mixed forest for the next 30 years. In addition, the division is involved in the production of beehives and bee colonies in the framework of their wood training workshop.
The Garant company used the proceeds from a raffle on the occasion of their 30-year anniversary to initiate a tree-planting campaign to reforest a nearby forest. Over an area of around two hectares, numerous spruces that were befallen by bark beetles had to be felled. In cooperation with the forest conservation organisation Schutzgemeinschaft Deutscher Wald and the Rockhausen forestry cooperative, Garant used the donated money to buy saplings that were planted with the help of numerous volunteers.
Consistently monitored goals
A certified power management system has made it possible to considerably simplify the monitoring at several companies. This has led to a greater sensitivity for energy savings. At the Plattling (D) site, for example, measurements are regularly taken in production via a state-of-the-art data acquisition system to identify any weak points and immediately replace inefficient consumers. At the Weinsheim (D) site, approximately 100 in-plant energy measurement points are in operation for the machines and the infrastructure.
At Prüm and at Garant, one energy team each is responsible for the current status and initiates improvements. Both companies determine energy key figures defined on a monthly basis and have their energy management systems externally checked and certified (TÜV and ICG) according to ISO 50001 on an annual basis. At Prüm and Garant, the energy and environmental management is also evaluated as part of the annual management review. The power consumption during operation at the Invado site in Poland is also regularly monitored and compared with the figures for the previous year. To check the effectiveness of the measures taken, the power consumption as well as the CO2 emission is determined for each manufactured product. Audits are additionally carried out at regular intervals. RWD Schlatter also has an energy management system: Targeted measures are derived from the analysed energy key figures that are collected at least once a year.
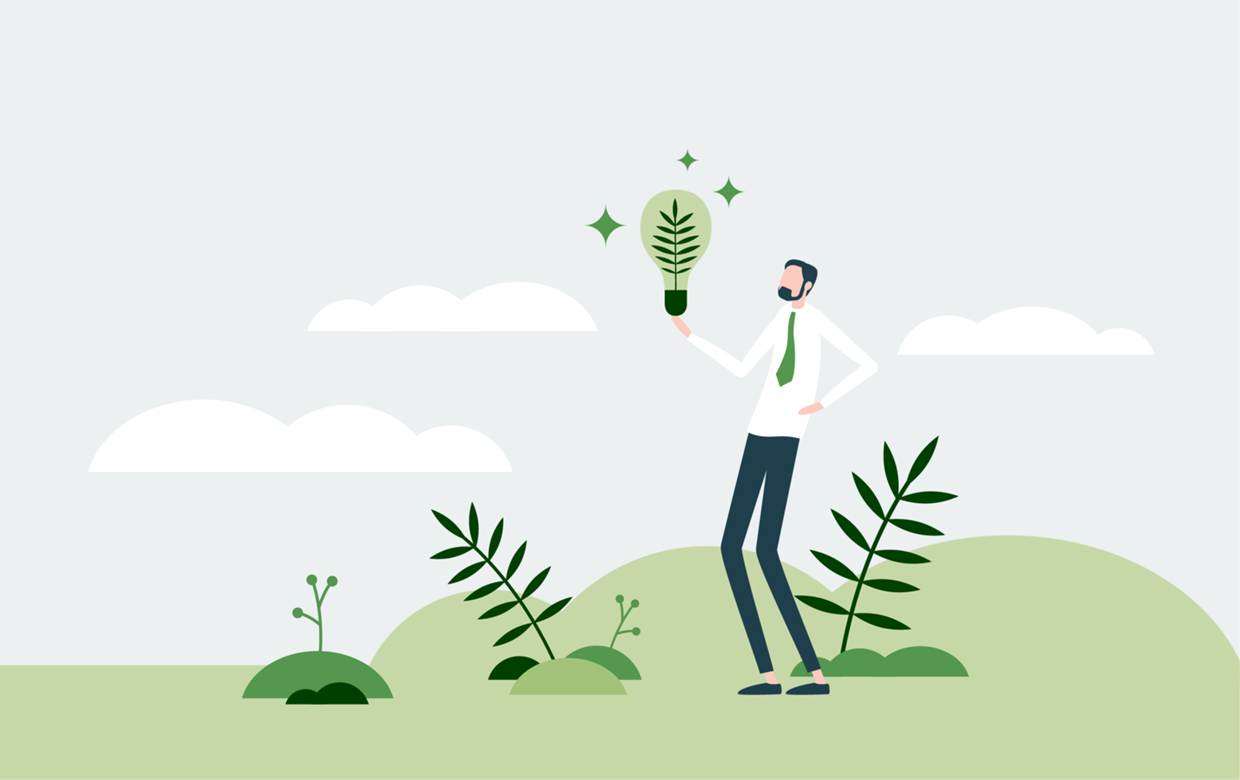