Procurement and supply chain
A sustainable supply chain brings a multitude of advantages. It creates innovation and drives the development of new management and production methods forwards. In addition, it improves reputation, strengthens customer relationships, and increases the interest of investors. A sustainable supply chain furthermore provides business benefits, since it improves the control of costs and resources and can thus lead to savings.
Nevertheless, negative effects can also occur due to risks within the supply chain. This concerns ecological aspects such as Scope 3 emissions as well as human rights violations. We are conscious of this challenge and strive for a higher transparency and duty of care with our suppliers.
The COVID-19 pandemic has made us aware of further direct and indirect effects during the past two years. The tail of the COVID-19 pandemic as well as the war in Ukraine made 2022 a year with multiple challenges in respect to the supply chain as well as energy prices. In this respect, we have intensified our efforts to cover the total requirements of value added. The context of procurement and supply chain not only comprises the total direct material (all materials that enter inventory through purchasing and procurement) but also indirect material such as tools and equipment, consultation and rent.
We preferably work with suppliers from the EU or the EEA; ideally with companies from countries in which Arbonia is active with production sites. In the reporting year, 78% of the purchasing volume was procured locally. This makes it possible to shorten transport distances and minimise the environmental impact. It additionally improves the control of production means compared to a partnership with suppliers from remote regions.
The topic of procurement and supply chain at Arbonia comprises on the one hand the procurement management for the most used materials and semi-finished goods – in other words, wood, steel, glass, and aluminium. On the other hand, the assessment of suppliers according to ecological and social criteria is also a part of this. At the same time, respect for human rights in the supply chain is of decisive importance. Since more than 95% of used materials are sourced from suppliers in Europe, a high standard is enshrined in law.
As a corporate group, we continuously raise awareness for ecological and social factors in direct and indirect purchasing. For this purpose, we train the employees of our purchasing departments in relation to sustainable supply chains, and we are working on a company-wide standard for supplier assessment in accordance with ESG criteria. In a first step, all direct suppliers are checked and prioritised according to the sales volume. As soon as this process is established, indirect suppliers will also follow according to the same assessment criteria. For the assessment of suppliers, external key figures (e.g. solvency, risk indicators, ESG ratings) are collected and combined with the internally generated data into a holistic assessment. In the reporting year, we primarily used ratings from EcoVadis for this for the first time. In respect to new regulations, the focus was on the procurement market of Germany and on large suppliers with more than CHF 1 million purchasing volume. As a result, we were able to cover around three quarters of the total purchasing volume in Germany or 54% of the global purchasing volume with EcoVadis or comparable ratings. For the coming years, we aim to integrate further large as well as smaller suppliers into the rating of EcoVadis. Suppliers from countries with an increased risk in relation to violations of human rights, child labour, and slavery are under observation regardless of the purchasing volume. However, these make up less than 2% of the global purchasing volume. Suppliers without an external certificate have to guarantee in a suitable way, for example, with a code of conduct that human rights are respected and that child labour and forced labour in particular are prevented.
As Arbonia, we have also had ourselves assessed by EcoVadis in the reporting year and achieved a bronze rating. This means that we are among the top half of all assessed companies. In the medium term, we want to improve this rating especially in the area of sustainable procurement through training and new guidelines.
In Germany, the Bundestag passed the Supply Chain Due Diligence Act (LkSG) in June 2021, which provides a legal framework for the responsibility of companies along the entire supply chain. This is relevant for all Arbonia companies active in Germany. They are evaluating the specific impacts of the new legislation and initiating corresponding compliance measures. The companies active in Switzerland have also initiated a comparable process to determine the implications of the counterproposal to the corporate responsibility initiative, the provisions of which went into affect on 1 January 2022 and will be applied for the first time in the reporting year 2023.
In addition, Arbonia has developed a Supplier Code of Conduct, which is to be successively extended to all suppliers if possible and is already part of orders. In this, Arbonia expressly commits itself to the Universal Declaration of Human Rights of the United Nations, the UN Convention on the Elimination of All Forms of Discrimination Against Women, and the UN Convention on the Rights of the Child.
Heating, Ventilation and Air Conditioning Division
Increased requirements – new measures
An intensified procurement of sustainable products is a matter of course for the entire HVAC Division. The pilot project for procuring decarbonised steel (with Green Steel certificate) for the production of steel panel radiators at the Plattling (D) site was successfully implemented in the reporting year. The division is currently focused on a concerted approach between sales and marketing for a green steel panel radiator strategy.
In respect to waste management, the Corbetta (IT) site has concluded a formal agreement with the suppliers to formalise all aspects (disposal licenses, information on the type, volume, and costs of the waste etc.). At the Dilsen (BE) site, it was possible to reduce the number of lorries used through a consistent optimisation of the logistics and logistics partners. In the packaging area, Sabiana has launched programmes for different products for which the packaging has a great effect on the costs and disposal. For example, the company is trying with its suppliers to introduce reusable containers, replace conventional wooden pallets with pallets made of corrugated board, and reduce waste with component packages.
Clear responsibilities in regard to procurement and supply chain
In close coordination with the customers and the marketing and sales departments, products are to be developed that can be manufactured more sustainably. The main goal of Sabiana remains certification in accordance with ISO standard 14000, which assesses the affects of the supply chain on the environment. For this purpose, the company assigns clear responsibilities, creates regular exchange formats and develops a status report including key performance indicators (KPIs). Sabiana monitored the progress, results, and achievement in smaller projects (delivery agreement, RoHS, REACH, 3TG etc.) monthly during the reporting year and properly registered them with position reports. In this connection, the head of logistics has the objective of monitoring transport costs monthly and optimising them in relation to the value of the transported goods.
Doors Division
The companies of the division pay attention to consistent certificates of origin for wood, among other things. At RWD Schlatter, a new timber trade regulation specifies a PEFC share of 80%; for FSC-certified wood, the share is 20%. At Invado, 100% of the wooden panels are made of raw material of European origin (EUTR documents). A complete monitoring of the used chemicals is also part of the consideration. In this way, the division avoids toxic substances and replaces them with less problematic materials. Additionally, the division is gradually changing over to ecological packaging materials such as cardboard and paper and is increasingly eliminating plastic or Styrofoam. Attention is also paid to recycling of the packaging. As a result, Kermi Sanitary Equipment in Plattling (D) was able to avoid 600 km of wooden panels in the reporting year, replacing them with cardboard. At RWD Schlatter, residue from Sonitus cores was used as an intermediate layer for transport.
Measures in supplier management and in logistics
On the customer side as well, corresponding audits are increasingly being carried out to determine whether the Doors Division complies with sustainability criteria. For example, the customers of Invado regularly check what materials the company uses to manufacture doors and frames and where the raw materials come from. For this reason, the division prefers to work with suppliers who have proven themselves for years. At the same time, initiatives for avoiding or recycling production waste are becoming more and more important. Ultimately, conserving resources also has a positive effect on profitability. For this purpose, the division carries out internal as well as external audits in the areas of quality, social issues, and energy efficiency. The expansion of a strategic category management is therefore being continued. This continually collects and evaluates market information in order to react to potential risks in the supply chain early on.
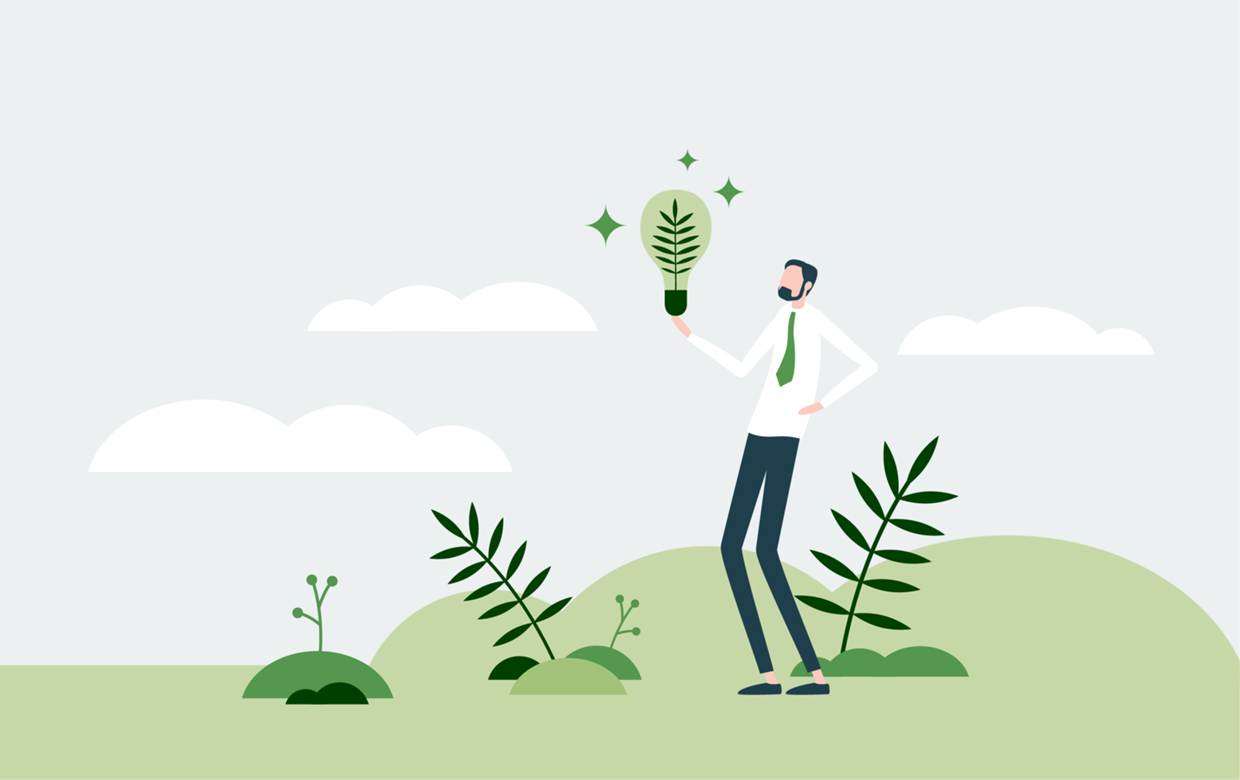