Resource efficiency
At Arbonia, it is our declared objective to conserve natural resources. For this reason, we are pursuing a foresighted resource management, avoid waste, and reduce material consumption as well as rejects. We measure the quantity of waste and analyse the error costs in order to assess the effectiveness of the measures. The energy- and material-efficient production based on a good resource management simultaneously reduces manufacturing costs and thereby increases competitiveness. Arbonia therefore strives for energy and material savings in the development of new products as well as in the improvement of existing products. The waste resulting at the company is consistently separated, pretreated where necessary, and then recycled. The companies of Arbonia regularly check how resources can be used even more carefully – for example, through clever product design and a production that is as free of defects as possible. For this purpose, we have issued a water policy and a waste policy for the entire Group that went into effect on 1 January 2022.
The subject of sustainability certificates for the manufactured products is becoming increasingly relevant: More and more customers are demanding low-pollutant materials and attach importance to a certification. Furthermore, many products already go through a pollutant test nowadays and are correspondingly certified according to the guidelines of eco-INSTITUT.
On the basis of lean manufacturing, quality can be increased and thus the number of complaints reduced. An improved quality management pays off towards the overriding aim of strengthening and expanding the market position through innovative and reliable products. Improvements in manufacturing technology are equally a matter of course as a continuous modernisation of the machine park and a targeted selection of suppliers for a constantly high raw material quality. Significant factors also include a continuous improvement of personnel qualifications, cross-company implementation of all measures, and the transfer of quality responsibility to employees.
Key figures for resource efficiency
The figures for commercial and hazardous waste cover all manufacturing companies in the Arbonia Group as well as the headquarters in Arbon, Switzerland. Pure distribution companies were not included. The survey method was changed, which is why the values for 2020 and 2021 are not comparable. The waste treatment and disposal at Garant was changed in 2022, resulting in significant shifts within the survey methods.
Key water consumption values
The water consumption was surveyed in 2022 for the first time, which is why no comparative values are given.
Heating, Ventilation and Air Conditioning Division
Continuous resource minimisation and recycling
The goal of the HVAC Division is to minimise material use during production. As a result, the error costs within the division are to be reduced to less than 1% of the annual turnover – while simultaneously increasing productivity. In addition, the division wants to use more recycled materials in all areas. A decrease in waste and the associated direct and indirect costs is also being pursued. The quantity of products that are disposed of through waste incineration and in landfills are also to be analysed and minimised. Last but not least, the division also makes an important contribution to the careful use of resources with its products. Steel radiators, for example, are nearly completely recyclable and can be reused at the end of their life. In the production of radiant panels, less material is now required due to an improved product design; the same holds true for heat exchangers.
Examples for an efficient use of resources
In the reporting year, it was possible to keep reject and error costs constant. In Plattling (D), the current projects for reducing panel thicknesses were advanced. The greatest challenge turned out to be maintaining the required pressure stability. At the Stříbro (CZ) site, the packaging was optimised: Instead of foil and Styrofoam, packages of recycled cardboard are now being consistently used. In Corbetta (IT), it was possible to significantly reduce the resulting copper scrap. A new ultrafiltration system allows sustainable water treatment and thus leads to a reduction in water consumption. During the reporting year, the site also introduced a consistent waste separation and recycling programme in the offices as well as in production. In Serbia, the division installed various workstations to optimise all process steps further – for example through digital solutions. The objective is to reduce waste by using scrap for production – for example for metal plates and profiles.
Doors Division
Resource efficiency along the entire value chain
Resource efficiency is also relevant for the Doors Division over the entire value chain. In the reporting year, it was possible to lower the consumption of natural gas by 33% and reduce waste by 29%. Water consumption was measured for the first time with reliable figures. To optimise the material consumption and avoid waste, a resource-friendly manufacturing is already pursued during development. The use of old or common parts is also checked in this phase. Arbonia Glassysteme (formerly GVG) collects its waste glass and delivers it to the manufacturing plant, reducing energy consumption in production.
The topic of resource efficiency is closely linked to product quality in the Doors Division – because high-quality products not only mean fewer rejects but also fewer complaints and thus higher customer satisfaction. At the division, reject and error costs are to be minimised by a continuous monitoring of resource efficiency.
An efficient use of required resources is achieved with stable, simple processes and the consistent reduction of rejects. Residual materials from production are recycled wherever possible. To improve resource efficiency, however, permanent information and training of employees – via shopfloor management or company meetings, for example – is decisive. In this way, Invado has succeeded in improving the economic and resource efficiency of the production processes with the introduction of the one-piece flow principle. The new process provides for a considerably lower time, material, and resource costs and thus a more effective production.
Ambitious targets
For the Doors Division, energy-related and environmental key figures play an important role in the planning and application of the future production technology. For example, Garant wants to lower the energy and resource consumption per manufactured part by at least 3%. This is to be achieved through greater efficiencies of the machines, preventive maintenance and continuous servicing, optimisation of the manufacturing control and minimisation of downtimes. RWD Schlatter wants to make processes more sustainable in the future. The company has already laid an important foundation for this with the state-of-the-art machinery. Particular attention is also to be paid to a further reduction of production waste and a consistent residue utilisation. Invado has set itself the goal of delivering doors and frames exclusively in cardboard packaging in the future. In addition, Invado wants to continue the principle of continuous improvement. The successful implementation of the SAP system (incl. production and fine planning as well as production control system) is to help with planning and following production processes (see introductory interview in the Cash chapter). Thanks to the integrated enterprise management software, Invado can monitor the production more efficiently, identify the places that produce the most waste, and initiate data-based improvement measures. The companies of the division want to reduce their inventories and improve delivery accuracy. The targets are also monitored through monthly tracking, among other things.
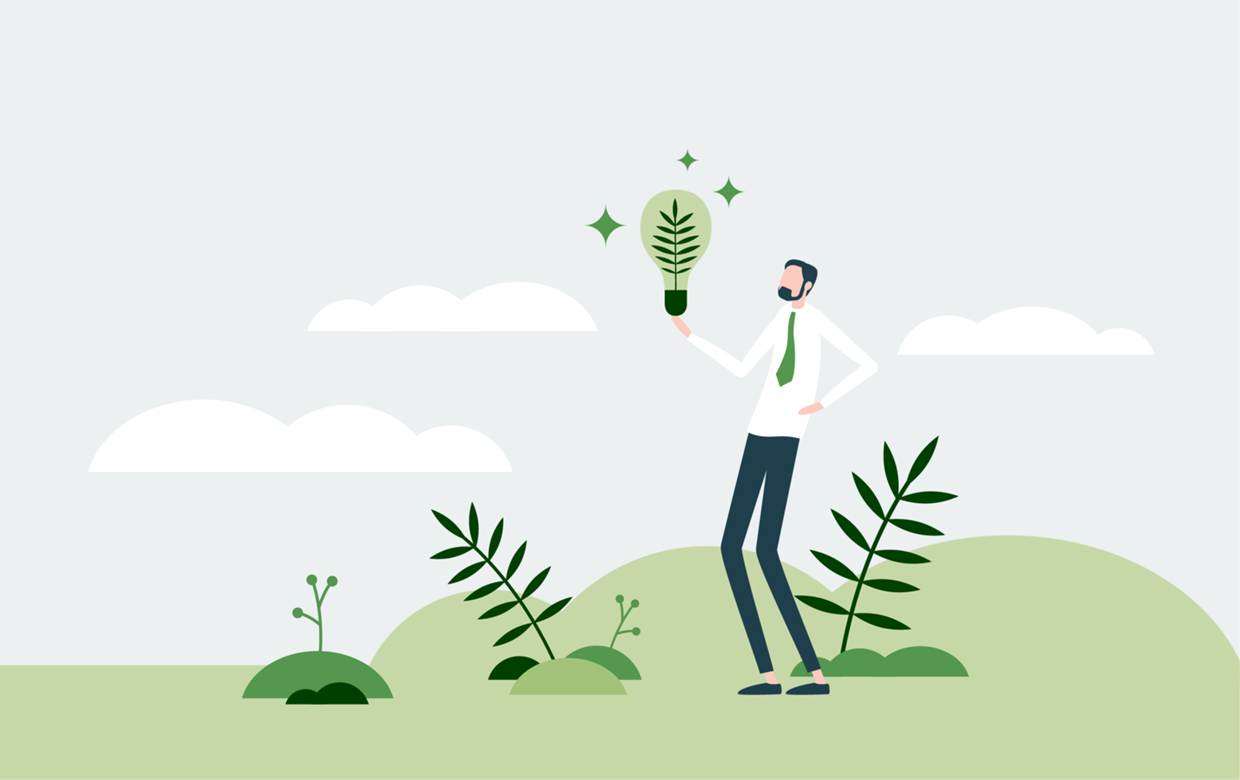