Use of resources and circular economy
Article 964a ff. Code of Obligations
Concept and due diligence
Our declared objective is to conserve natural resources and establish a materials cycle that is as circular as possible, thus also cutting down on the amount of energy required for transporting and processing those raw materials. Various areas of the company share responsibility for the cross-cutting issue of resource management. Product Management and Development have the task of designing products that can be produced in as resource- efficient a manner as possible. The production managers are responsible for ensuring that processes are designed with resource efficiency and a circular economy in mind. Within this context, the divisions and companies of Arbonia have also set themselves their own targets in some cases. For example, the Climate Division intends to minimise the use of materials in production and reduce error costs to well below 1% of annual turnover. In the Doors Division, Garant has set itself the target of reducing energy and resource consumption per manufactured part by at least 3% per year. A waste policy has been in place across the entire Group since the 2022 financial year. This policy aims to raise awareness of consistent separation of operational waste, stipulates that production must be reviewed with regard to resource-efficient processes and states that volumes of waste must be measured.
Measures including evaluation of effectiveness
The introduction and expansion of digital systems supports resource-efficient operations at Arbonia, which led to less waste, reduced water consumption and optimised use of resources in the reporting year. Arbonia has established a forward-looking resource management system, focusing on high quality and production that is as free of defects as possible in order to prevent rejects and complaints. Energy and material savings are to be taken into consideration when developing new products and improving existing ones. Usable production waste or old parts are used again in manufacturing where possible. In 2023, the divisions were able to increase the proportion of recycled materials and replace plastics in both products and packaging with cardboard. At the same time, the proportion of recyclable products and the use of recycled packaging are increasing and more and more products are undergoing sustainability certification. Arbonia is also keen to protect resources when it comes to its construction activities – for example, by using domestic woods where possible. In 2023, RWD Schlatter received a sustainability award for the use of Swiss wood in its construction work.
Material risks and how they are handled (own scope of business and, where applicable, business relationships)
Market distortion and supply chain problems can cause (raw) material and freight prices to rise, or result in products and services being unavailable. It is not possible for higher manufacturing costs to be passed on to the customer in full, or they cannot be passed on quickly enough, resulting in additional expense, delivery delays, a decrease in revenue and loss of margins.
Key performance indicators
Our key performance indicators relate to the use of resources and the circular economy as well as water consumption, waste by disposal method, waste and error costs (see table further down).
Arbonia is keen to conserve natural resources and is pursuing a forward-looking resource management strategy in line with the principle of continuous improvement. The company is also using digital solutions to support the planning and implementation of production processes. Energy- and material-efficient production based on good resource management simultaneously reduces manufacturing costs and thereby increases competitiveness. We therefore strive for energy and material savings in the development of new products as well as in the improvement of existing products. The use of old or common parts is also checked in this phase. The aim is to achieve a decrease in waste and the associated direct and indirect costs. We measure the quantity of waste and analyse the error costs in order to assess the effectiveness of the measures. The waste resulting at the company is consistently separated, pretreated where necessary and then recycled. The quantity of products that are disposed of through waste incineration and in landfills is also to be analysed and minimised. The companies of Arbonia regularly check how resources can be used even more carefully – for example, through clever product design and production that is as free of defects as possible. The goal here is to minimise reject and error costs by means of continuous monitoring.
The subject of sustainability certificates for the manufactured products is becoming increasingly relevant: More and more customers are demanding low-pollutant materials and attaching importance to certification. Furthermore, many products also go through a pollutant test and are certified according to the guidelines of eco-INSTITUT.
On the basis of lean manufacturing, quality can be increased and thus the number of complaints reduced. Improved quality management will contribute to the overriding aim of strengthening and expanding the market position through innovative and reliable products. Improvements in manufacturing technology are a matter of course, as is continuous modernisation of the machine park and a targeted selection of suppliers to ensure consistently high raw material quality. Significant factors also include continuous improvement of personnel qualifications, cross-company implementation of all measures and the transfer of quality responsibility to employees.
To ensure constant improvement, employees must be provided with information and training on a continuous basis – via shop floor management or company meetings, for example.
Key figures for resource efficiency
The figures for non-hazardous and hazardous waste cover all manufacturing companies in the Arbonia Group as well as the headquarters in Arbon, Switzerland. Pure distribution companies were not included. The treatment and disposal of waste at Garant was changed in 2022, resulting in significant shifts within the survey methods.
Key water consumption values
Climate Division
Continuous resource minimisation and reuse
The Climate Division has set itself the target of minimising the use of materials in production. The aim is to reduce error costs to well below 1% of the annual turnover – while simultaneously increasing productivity. In addition, the division wants to use more recycled materials in all areas. Within the scope of the digitisation projects, Industry 4.0 and Logistics 4.0 are leading to considerably increased efficiency with a reduced use of resources.
Last but not least, the division is also making a contribution to the careful use of resources with its products. Steel radiators, for example, are nearly completely recyclable and can be reused at the end of their life. In the production of radiant panels, less material is now required due to an improved product design; the same holds true for the production of heat exchangers.
Examples for an efficient use of resources
The division has a number of initiatives and projects aimed at contributing to resource efficiency and a circular economy. In the reporting year, for example, reject and error costs were reduced beyond the set target, resulting in error costs of just 0.85% in 2023.
In Stříbro (CZ), progress was made with the ongoing projects aimed at reducing pipe wall thicknesses. In Corbetta (IT), further improvements were made with regard to the proportion of fully recyclable products and packaging. Furthermore, rather than packing heat exchangers in single-use packaging when transporting them internally between the production plants, they are now packed in a recycled plastic box which can be used for 10 years. This initiative, which began in 2023 and will be completed in 2027, will gradually reduce the quantity of plastic and paper materials used in internal packaging. By 2027, the aim is to have completely eliminated the 336 kg of plastic used in 2023, as well as reducing the number of wooden pallets in use. The company is switching to plastic pallets for internal transport, which means that the 25 210 kg of wood used in 2023 will be reduced to zero by 2027. A further aim is to reduce the use of plastic and cardboard in production and logistics processes as well as in administrative tasks in the company’s offices.
Sabiana’s goal is to integrate recycled materials into its operations. One example of this is the use of sintered expanded polystyrene (recycled EPS instead of “pure” EPS) as padding in packaging. The proportion of recycled EPS in use is currently minimal, but the division is planning to implement a gradual substitution between now and the end of 2027. By then, 60% of the packaging material should feature 35% recycled EPS and the remaining 40% should feature 15% recycled EPS. The integration of recycled material is also being evaluated in relation to other internal assembly/production processes.
Furthermore, EPS is to be replaced with cardboard within the packaging process in order to reduce the amount of non- renewable packaging materials in certain product lines. Using cardboard instead of plastic in product and packaging components has already reduced the amount of plastic used in several product families. In total, 21 440 kg of plastic was saved in 2023. The ultrafiltration system installed in 2022 allows water to be treated, thus reducing water consumption. Sabiana is also keen to reduce the number of plastic water bottles used by employees and has therefore provided free water coolers in the offices and production facilities.
In Serbia, the division has installed various workstations to optimise all process steps further. The objective is to use scrap for production – for example for metal plates and profiles. In 2023, the Plattling (D) site initiated a project which involves filtering the water from test basins and reusing it, thus saving up to 60% fresh water.
Doors Division
Working towards an ambitious target
For the Doors Division, energy-related and environmental key figures play an important role in the planning and application of the future production technology. For example, Garant wants to lower the energy and resource consumption per manufactured part by at least 3% per year. This is to be achieved through greater machine efficiency, preventive maintenance and continuous servicing, optimisation of manufacturing control and minimisation of downtimes. In 2023, digital solutions allowed the companies in the Doors Division to reduce their inventories and improve delivery accuracy. The targets are also monitored through monthly tracking, among other things.
With regard to glass solutions from Kermi, a shop floor management system introduced in 2023 has improved production planning, thus reducing excess production and inventories. RWD Schlatter is also working to make its processes more sustainable in the future with the help of its state-of-the-art machinery. Particular attention is also to be paid to the continued reduction of production waste and consistent use of leftover materials. Invado has set itself the goal of delivering doors and frames exclusively in cardboard packaging in the future. By the end of 2023, the company had managed to replace around two thirds of the polystyrene corner protection with cardboard. The plan for 2024 is for all corner protection to be made of cardboard.
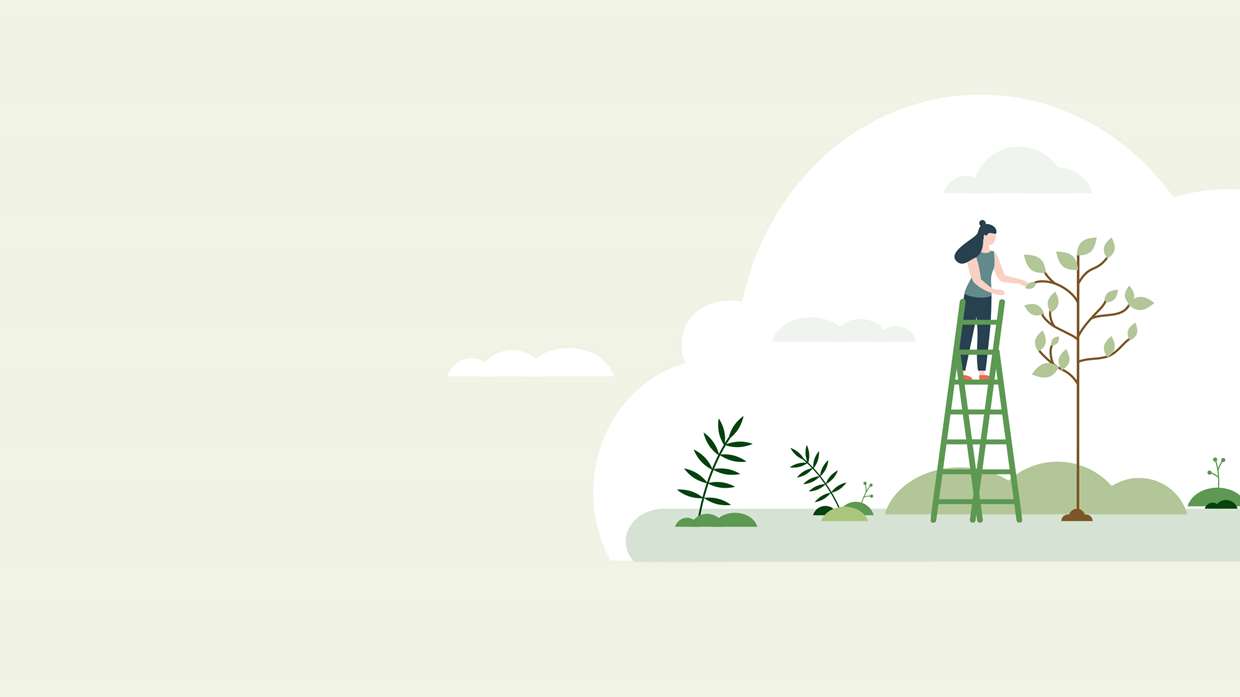